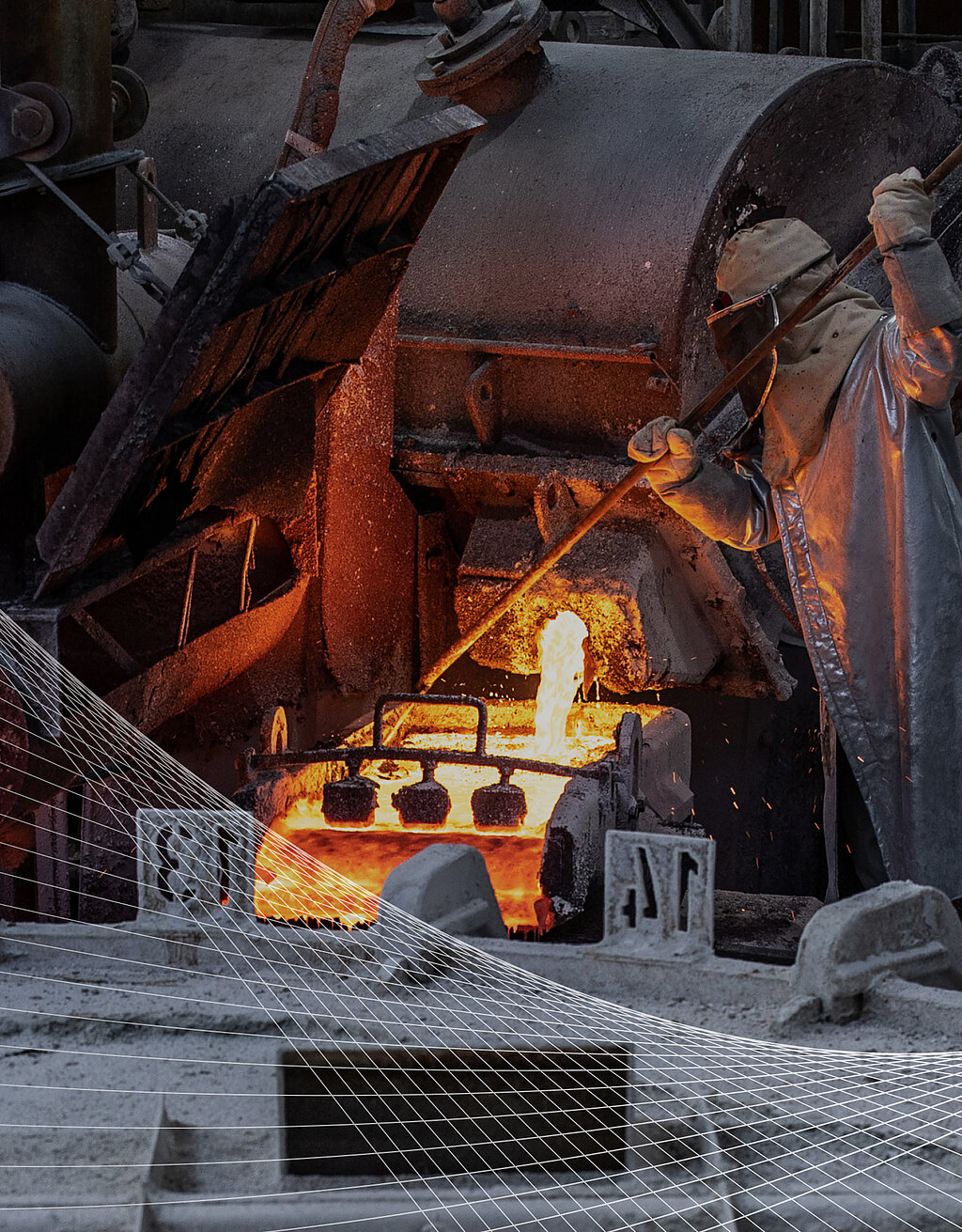
Expertise
New solutions, new markets
Our network serves as the foundation for innovations, and new technologies and markets. We use our metallurgical expertise to forge new paths: This is how we are shaping the future.
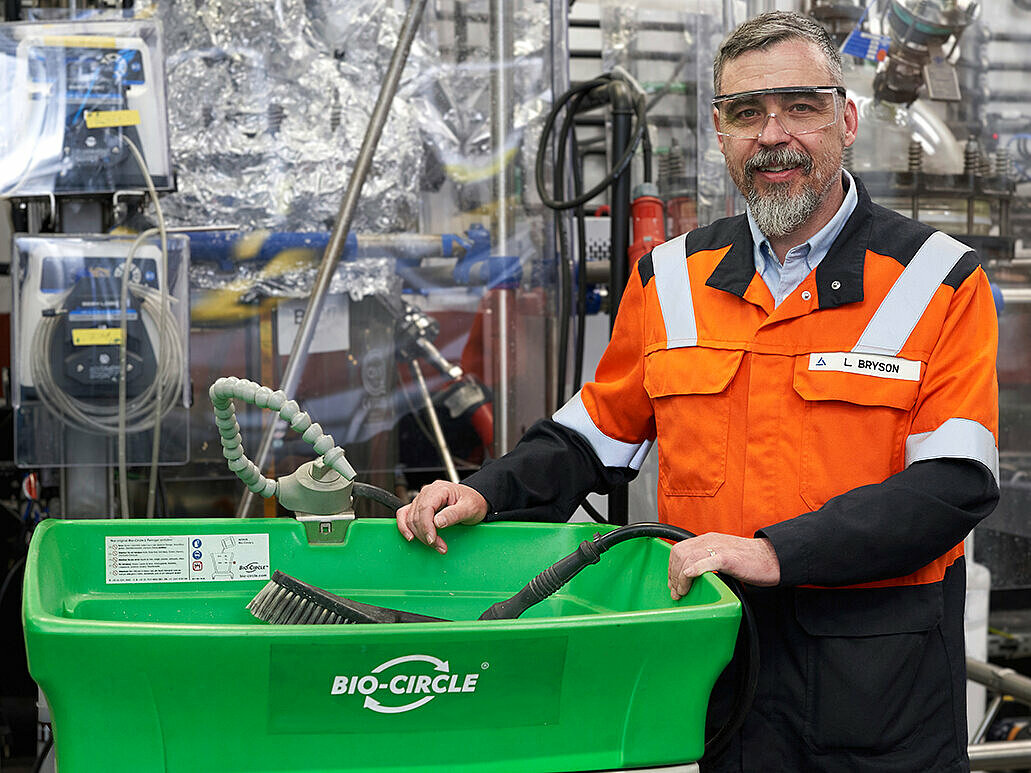
Innovative proprietary process
Black mass, green potential. These four words indicate a future growth area for Aurubis. Handling resources responsibly is central to our activities, and we pledge to keep valuable metals in the material loop. This is also true for electric cars. Demand for batteries for electric cars is on the rise — and with it the demand for valuable materials. This is where our recycling expertise comes into play: We have developed an innovative process to recover the maximum from old lithium-ion batteries so new products can be made.
Black mass is what is left over when end-of-life batteries are crushed, shredded and treated. The powdery substance contains valuable elements from the battery, including lithium, nickel, cobalt and manganese. In a relatively short period of time, we successfully developed a special technology at our battery recycling pilot plant at the Hamburg site that has since been patented. An innovative and exceptionally effective process: In our smelter network, we recovered around 95 % of the metals contained in batteries — including the light metal lithium, economically extremely important and limited to just a few mining regions worldwide. Scaling up the pilot plant to a demonstration plant for the first commercial activities is the next step at the Hamburg site.
A success based on our core expertise: the unique metallurgical skill of the Aurubis network, built on decades of extracting and recovering metals. Cables and connectors, cell modules, battery management systems — batteries are complex recycling materials. The mix of different materials is what makes battery recycling so challenging: The black mass is a complex amalgam. The battery cells contain a variety of chemical compounds, and a lithium-ion battery’s construction varies widely from manufacturer to manufacturer.
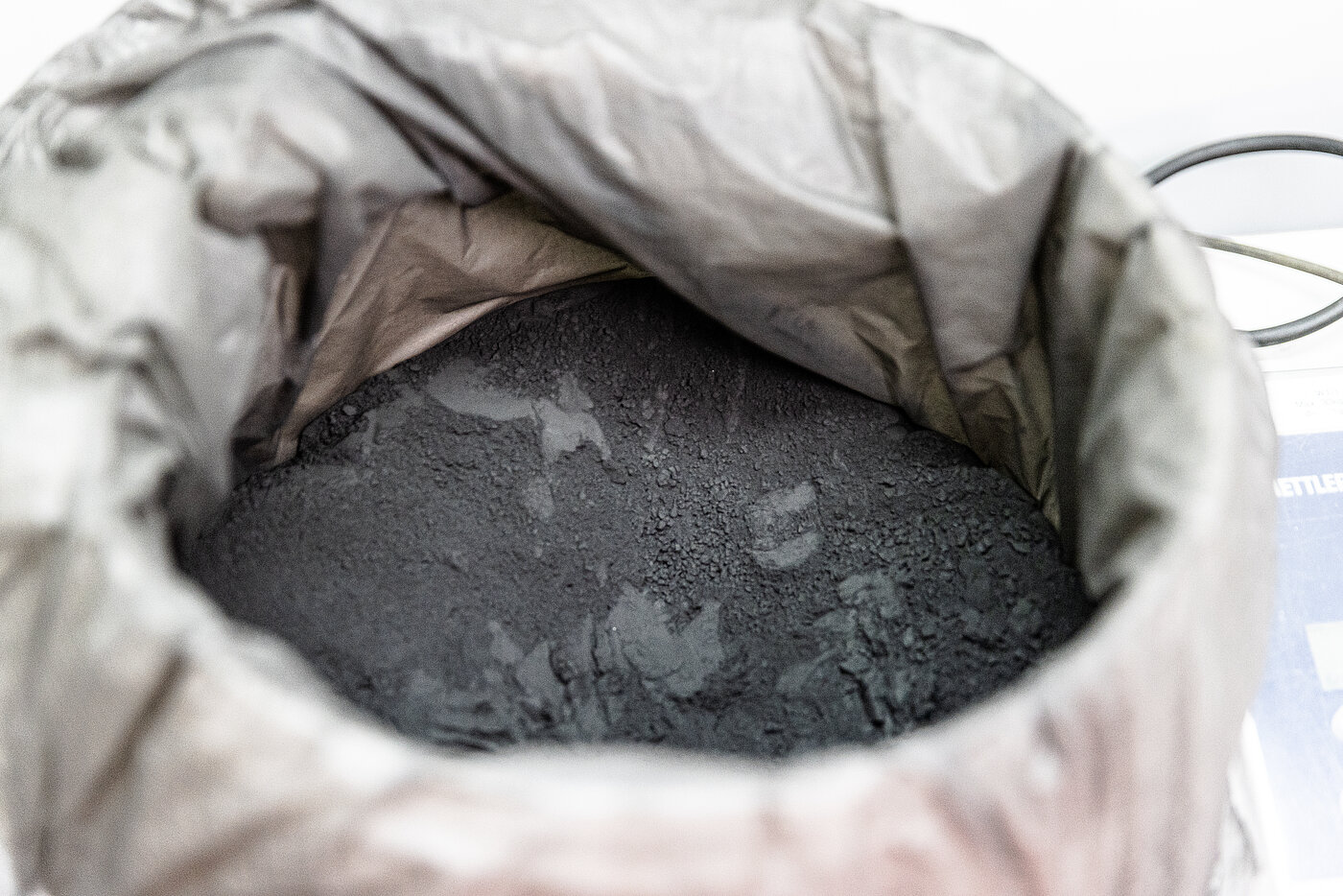
Around
95%
of the battery metals are recovered from the black mass
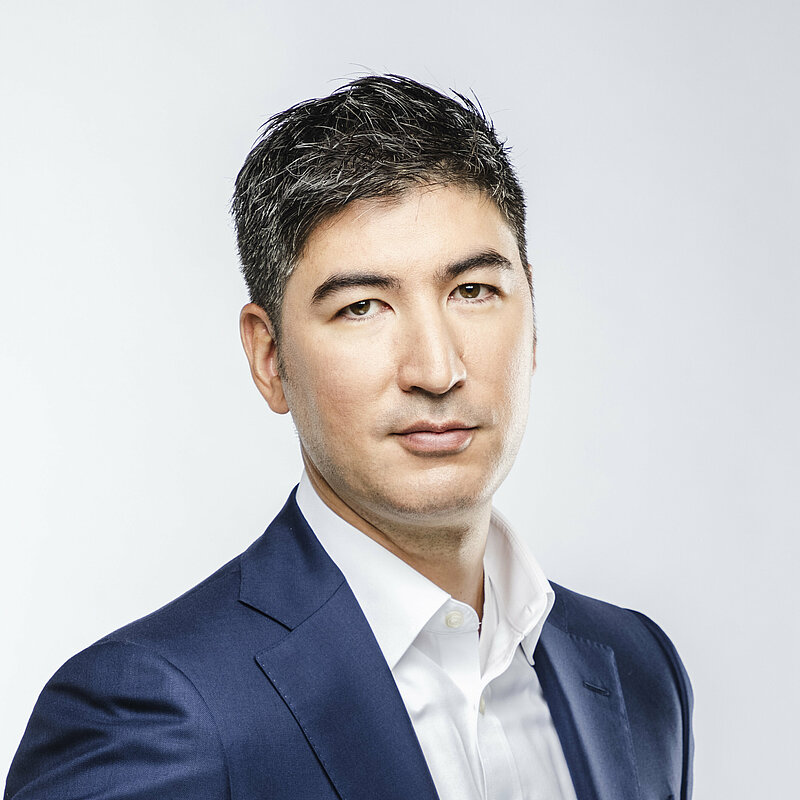
“Thanks to our metallurgical know-how and extensive operative experience, process development didn’t have to start from scratch.”
— Ken Nagayama, Head of Business Development for Battery Materials
Market ready
These are not new challenges for Aurubis. This is our everyday. And our core expertise in metallurgy fosters another success factor: speed. “Thanks to our metallurgical know-how and extensive operative experience, process development didn’t have to start from scratch,” Ken Nagayama, Head of Business Development for Battery Materials, says. “Quite the opposite. Based on Aurubis’ exceptional level of key expertise, technology development went quite fast, even with all the testing. The result: We’ll be ready to enter the market just when the market needs sophisticated solutions.”
Aurubis has all the prerequisites and skills needed to successfully recycle batteries: technology leadership in metallurgy, an integrated smelter network, and existing materials streams for most non-ferrous metals. In battery recycling, we are not only profiting from our integrated smelter network — we are also strengthening our network and optimizing our core business. What we have serves as a foundation for the new, and the new strengthens what we have — we’re closing loops here, too.
Decarbonizing our processes
To us, expertise means questioning the status quo and forging new paths — in energy, too. Transitioning to carbon-neutral production is a real challenge for an energy-intensive company. And we’re tackling it. We’re testing new, low-emission energy sources and constantly enhancing our facilities to drive the decarbonization of our processes forward.
In the future, our Hamburg plant will be one of the first copper smelters worldwide ready to use hydrogen instead of natural gas in anode furnaces. A technology with the potential to prevent many thousands of tons of CO2. In addition to the impact on the climate, upgrading the furnace area will boost the efficiency of our processes. The new equipment will be able to process larger amounts of metal concentrates and recycling materials — and extract more metals even more efficiently.
We have already proven that hydrogen can successfully be used in production: In a pilot project at the Hamburg plant, we were able to produce copper anodes using hydrogen (H2) instead of natural gas — the first use of hydrogen on an industrial scale — in 2021. At the moment, there isn’t enough green hydrogen to cover German industry’s huge demand at competitive prices. But we’re still driving research and expanding our H2 readiness. Aurubis is gearing up and will be ready to go when the energy market catches up.
Gray hydrogen
Produced using fossil fuels, generating CO₂.
Blue hydrogen
Produced using fossil fuels, but the CO₂ is captured and stored (CCS = carbon capture and storage) or further processed as a raw material.
Green hydrogen
Produced using only renewable energy, so no CO₂ emissions.
A willingness to explore technology and invest in innovation — we see these as critical answers to the rising demand for raw materials resulting from the green transformation. So we are consistently improving on our state-of-the art recycling technology. Our new pilot plant at our conventional recycling plant in Lünen is just the latest example; it allows us to recover metals essential to the energy and infrastructure shift even more efficiently. The number of different layers in the computers and other electronic waste processed there is growing — as is plastic content. This presents a problem for efficient, sustainable recycling. It isn’t always possible to separate plastics and metals economically. The heat value of plastic is too high for it to go into our furnaces, though, and, even more importantly, burning it generates CO2. So the high percentage of plastic results in a limitation of our production volume.
We’re turning this problem into a solution with our new pilot plant: It uses ultra-high-temperature-hydrolysis technology (UHTH) to convert plastics into a gas that can be used as a fuel. Solid carbon is produced in the process, which offers potential for new products — and with it a way to close more material loops. And finally, more recycling materials will ideally be processed efficiently in Lünen — generating more new raw materials for our smelter network.
We see an openness to know-how from other fields as an element of expertise. We are the first in the metal extraction industry to use innovative UHTH technology. “This investment in a technology from outside our industry is another example of our pioneering role in efficient and sustainable industrial production,” Verena von Weiss, Aurubis Lünen Plant Manager, says. “The new pilot plant isn’t just a chance to raise our site’s environmental performance to new heights and decarbonize our processes even further. It’s also a testament to our identity as a driver of innovation.” Lateral thinking, exploring the unknown — important building blocks at Aurubis.
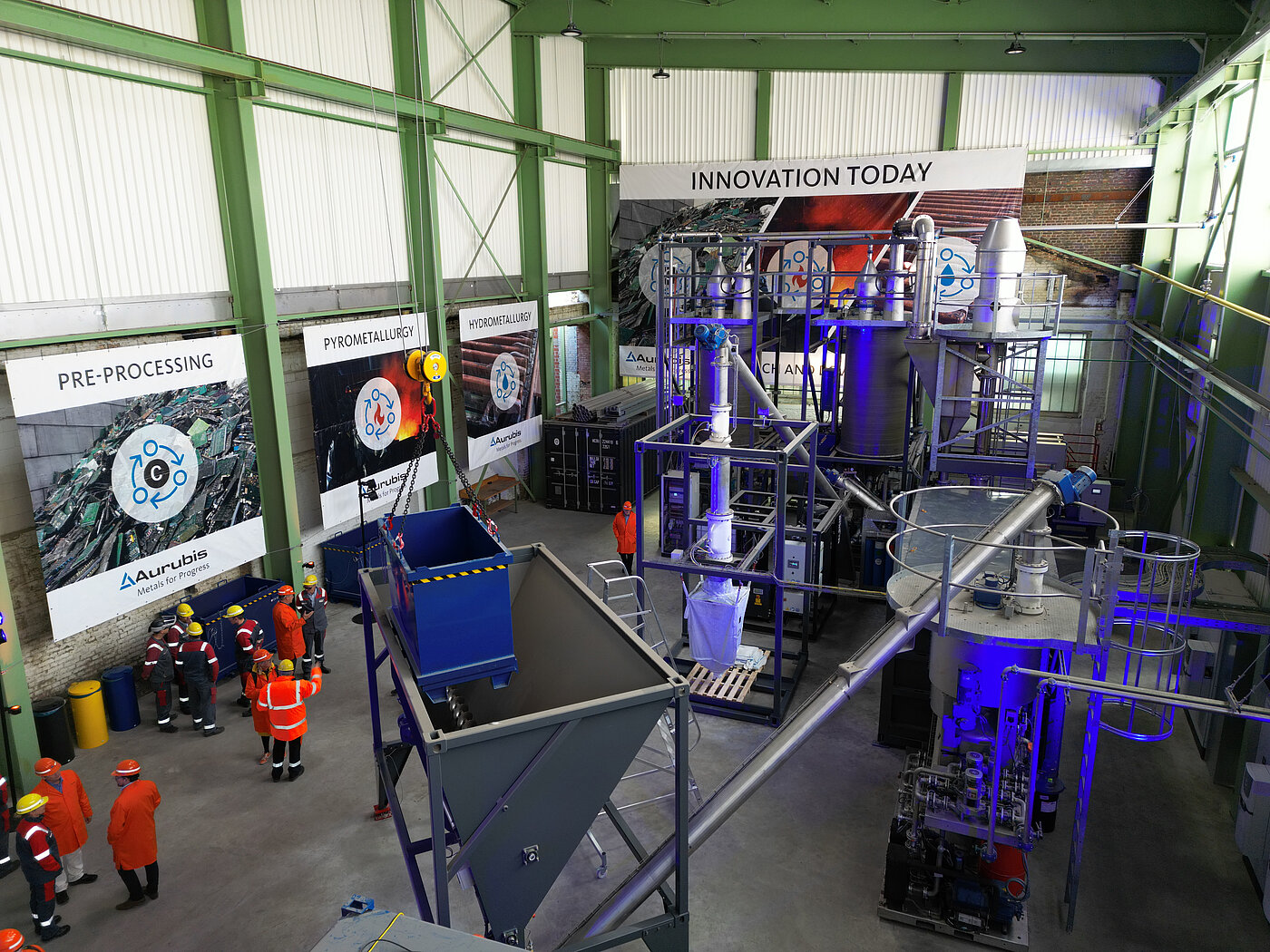
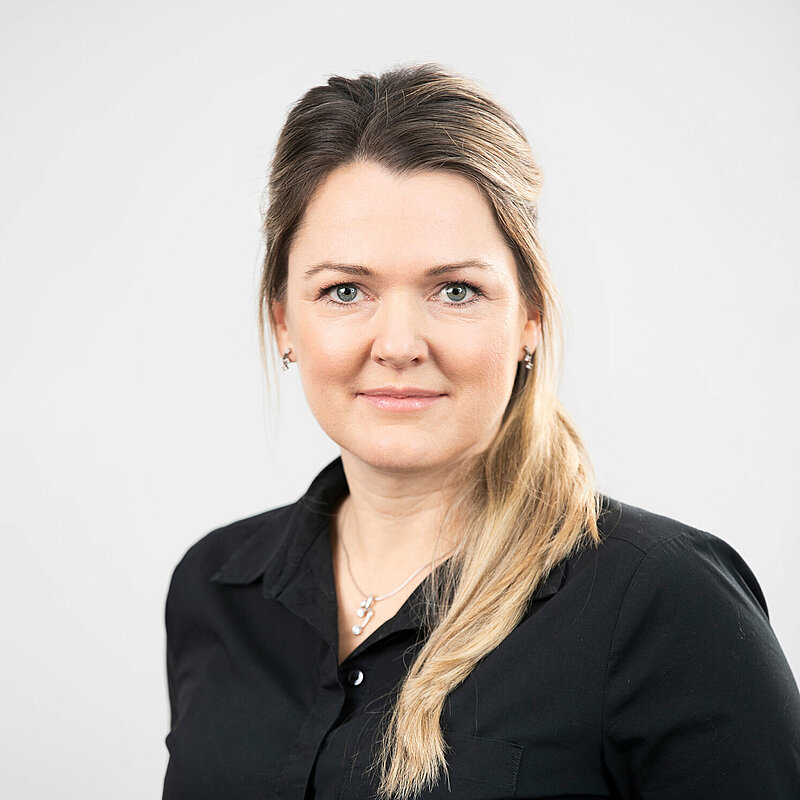
“This investment in a technology from outside our industry is another example of our pioneering role in efficient and sustainable industrial production.”
— Verena von Weiss, Aurubis Lünen Plant Manager
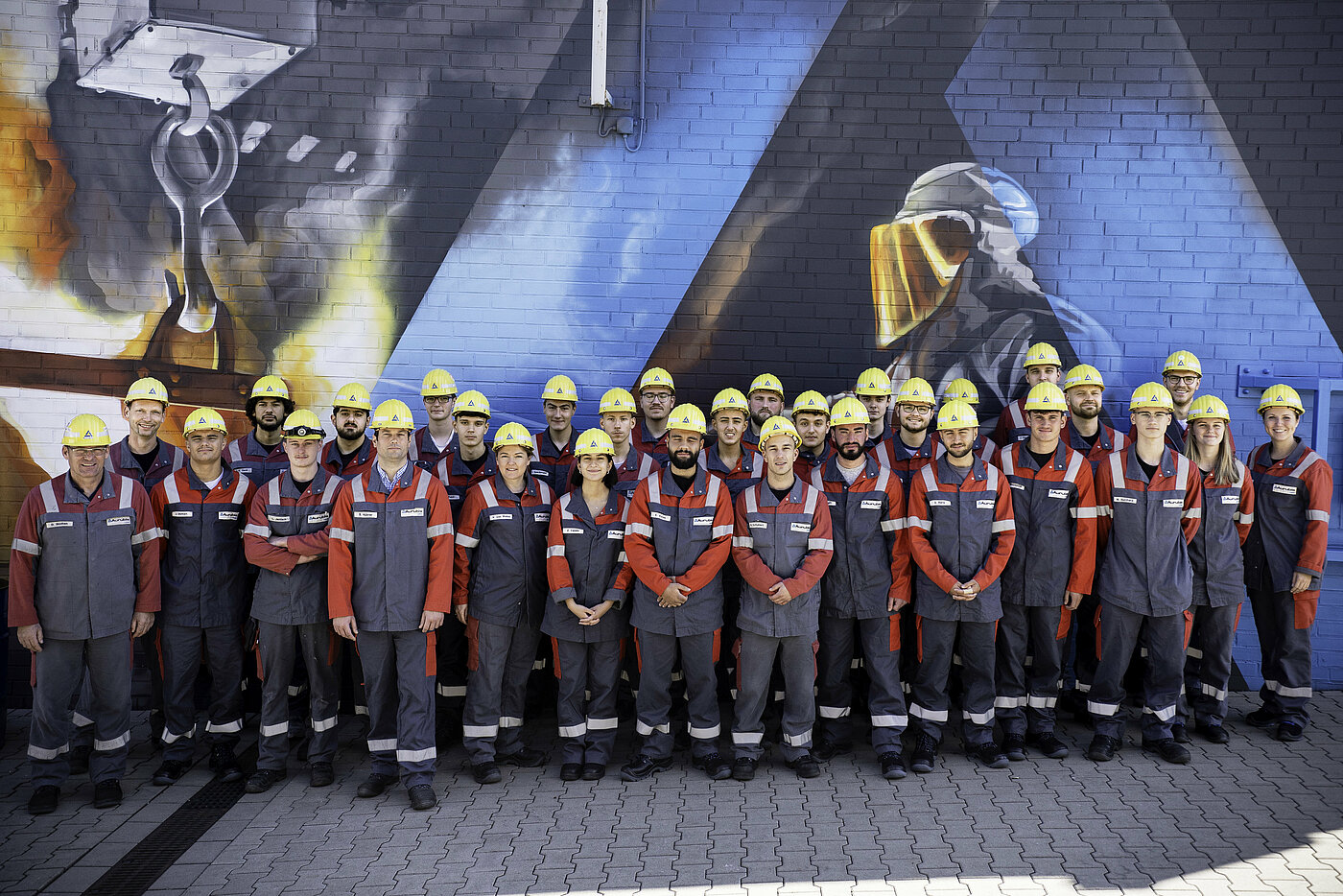
We offer training: our experts of the future
Educating our own experts is part of our company strategy. Our attractive range wins people over, despite the current shortage of qualified workers: In September 2023, 78 young people started their education in 13 professions and dual work/study programs at our Hamburg site, and 14 new employees started their training in seven specialized areas at the Lünen site. We are proud of the fact that over 85 % of apprentices have chosen to join the Aurubis workforce after training (in Hamburg) over the past ten years. We also promote professional exchange through networking — like our international network for students, student workers, and university interns — and offer young people struggling to find a foothold in life the opportunity to prepare for an apprenticeship in our industry.
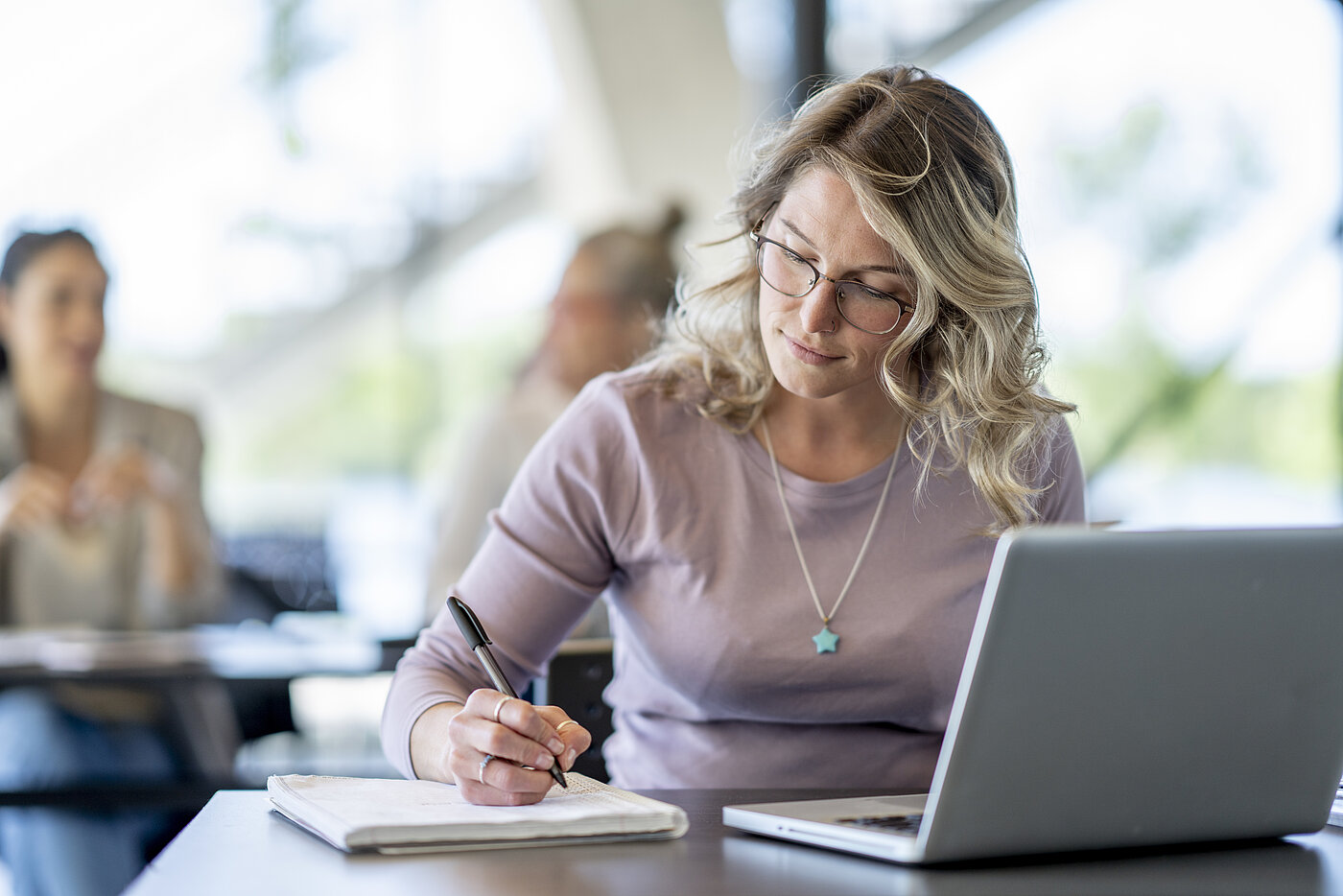
We offer a lifetime of learning: employee qualification
Lifelong learning is more than just a catchphrase at Aurubis. Our Learning Academy offers every employee throughout the Group a wide range of continuing education options and information: comprehensive training sessions on fundamental topics in the company, like “The Copper Story”, or about our strategy, and method tutorials and learning units on more specialized topics, like project communication and time management. Every employee can also take advantage of an allotment of 18 hours for continuing education per year.
We foster diversity: the foundation for good teamwork
A diverse workforce is the foundation for good teamwork, so we ensure everyone in the company is treated with fairness and respect. This mindset is laid out in our Code of Conduct, the Aurubis Human Rights Commitment, and the Aurubis Diversity Commitment. We see diversity as an opportunity to leverage a wide range of perspectives and viewpoints, cultural backgrounds, international experience, individual skills, and a diverse demographic mix to promote our corporate success.
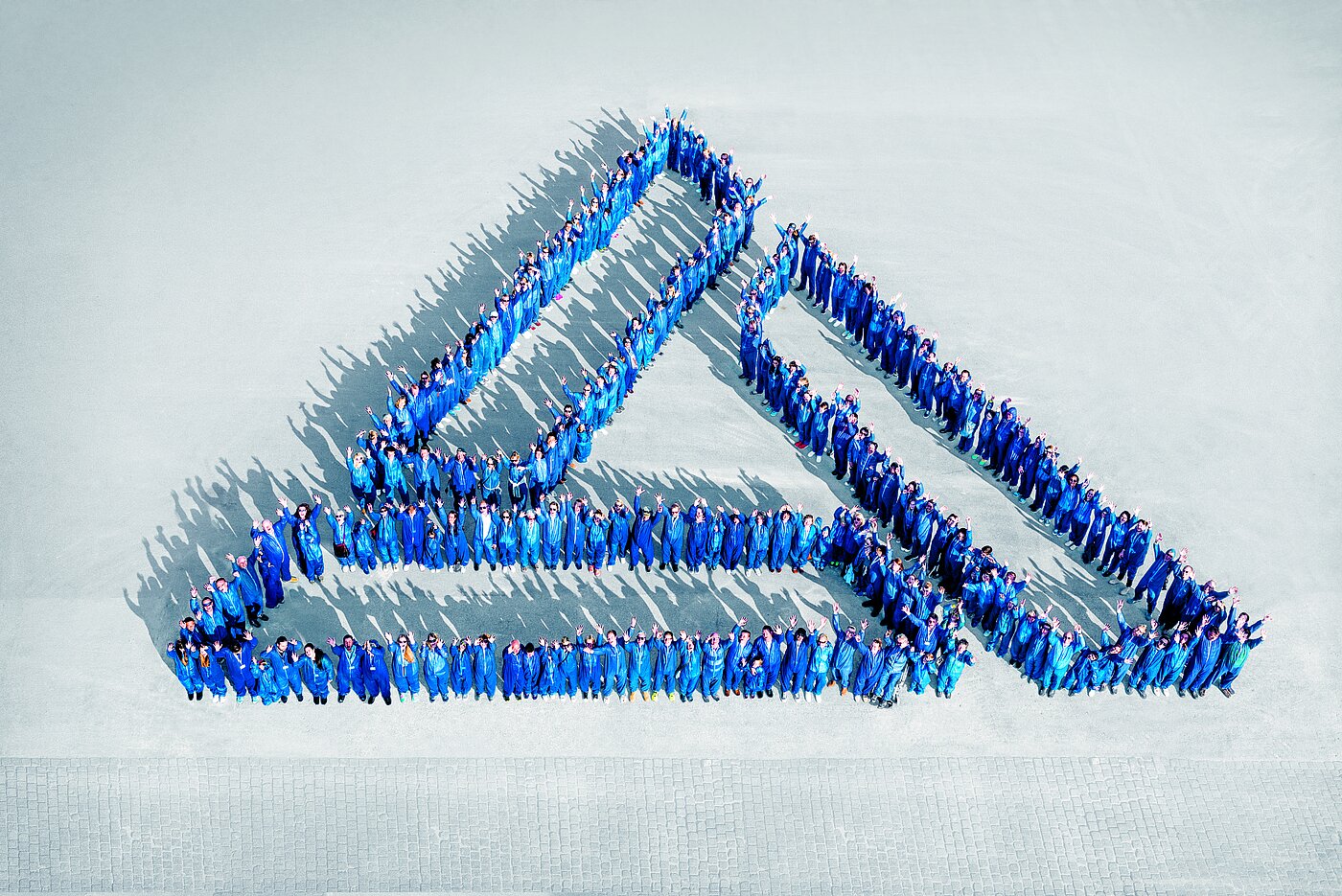
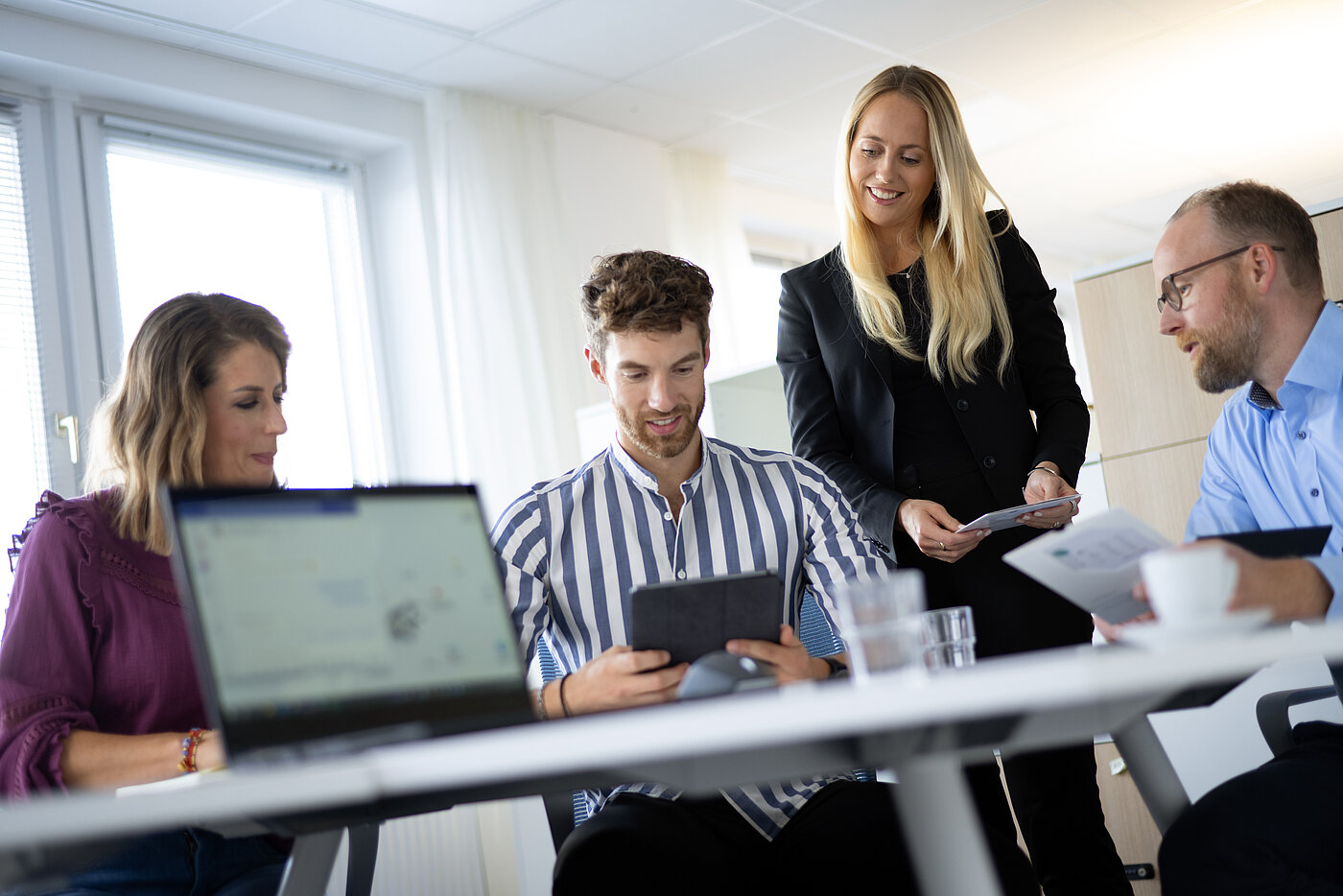
We work together: using multidisciplinary knowledge
We are improving every day to make sure we reach our goals. We take advantage of all the interdisciplinary expert knowledge from all divisions to arrive at the best results for Aurubis — and for the environment. One project in the secondary smelter Plant North (RWN) at our Hamburg site is a shining example of this. An expert team made up of colleagues from the plant, Environmental Protection, Controlling, and Production Planning is working on a new process for the electric furnace: The limestone input material currently used will be replaced by less expensive, carbon-free converter slag. This will cut costs, increase efficiency, and prevent CO2 emissions. This is just one example of how we are using our in-house expert knowledge to generate innovative power and to foster the circular economy.