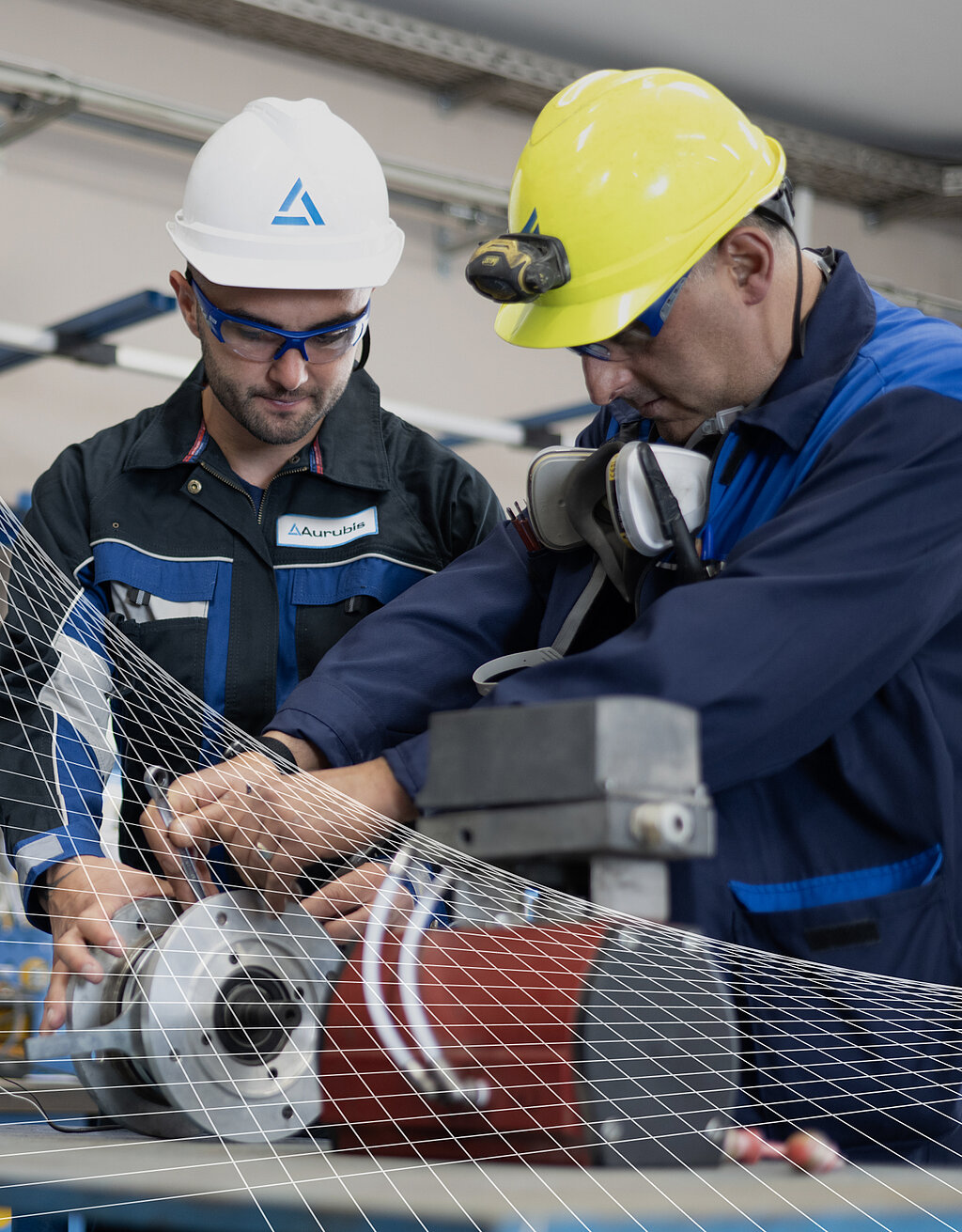
Optimization
Better, more sustainable, more efficient. Our focus: optimization
Aurubis already produces a number of its metals with less than half the CO2 emissions of its global competitors. But we won’t stop there. We want to continue improving to make our production carbon-neutral well before 2050. We’re investing not only in the growing recycling markets of the future, but also in energy efficiency, decarbonizing and maintaining our facilities, developing modern technologies, and digitalizing and automating our plants.
With a number of measures and projects, we’re continuously working on getting better in all aspects of sustainability at our smelter network sites. This has been verified by the CSR (corporate social responsibility) ranking issued by the EcoVadis rating agency: In 2023, we once again numbered among the best 1 % of companies in the non-ferrous metals industry worldwide. Aurubis improved by five points, particularly in the “Sustainable Procurement” category, and was classified a “leader” in carbon management. We have linked most of our financing instruments to the development of the EcoVadis rating, an indication of just how seriously we take our sustainability targets.
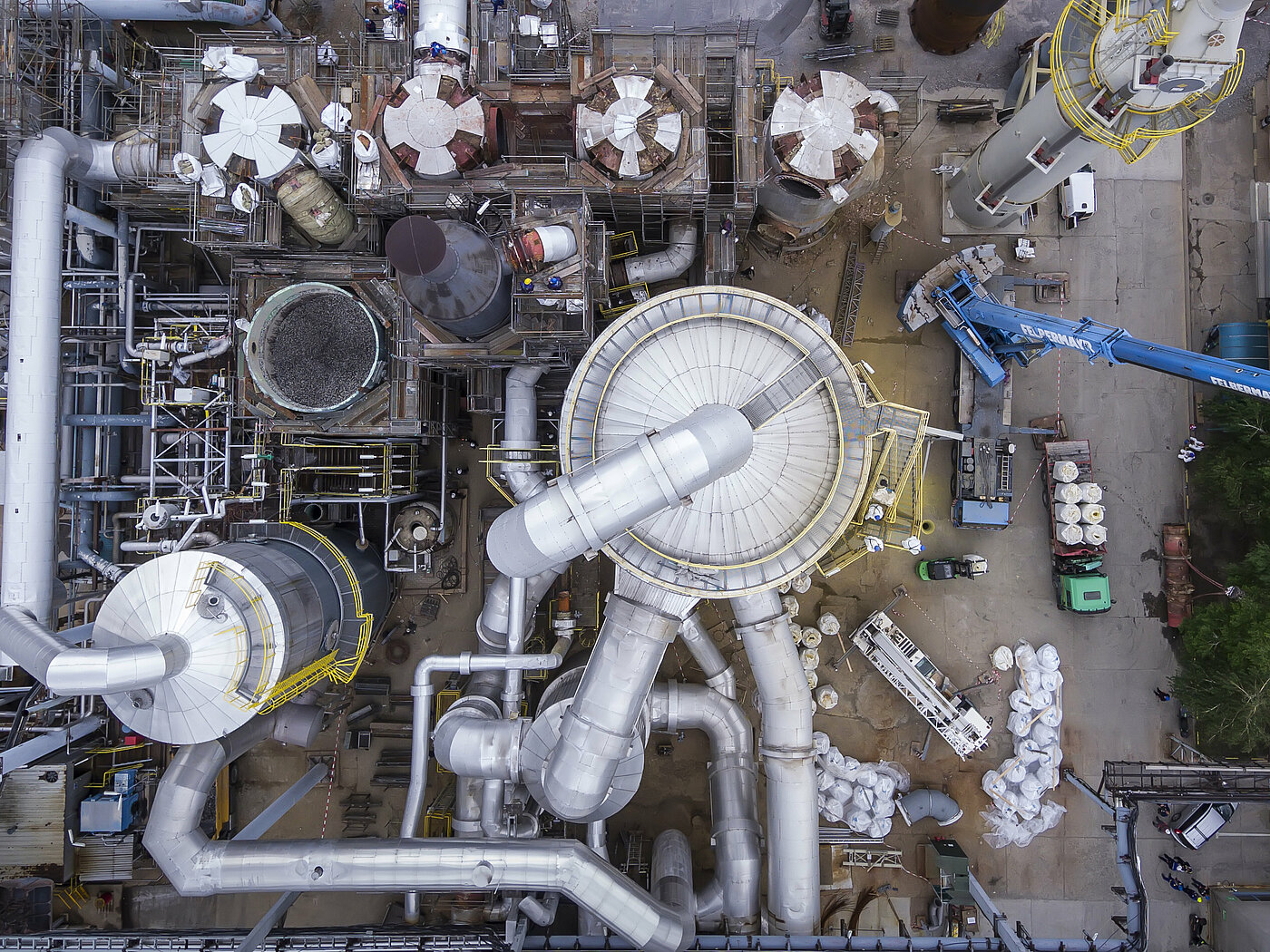
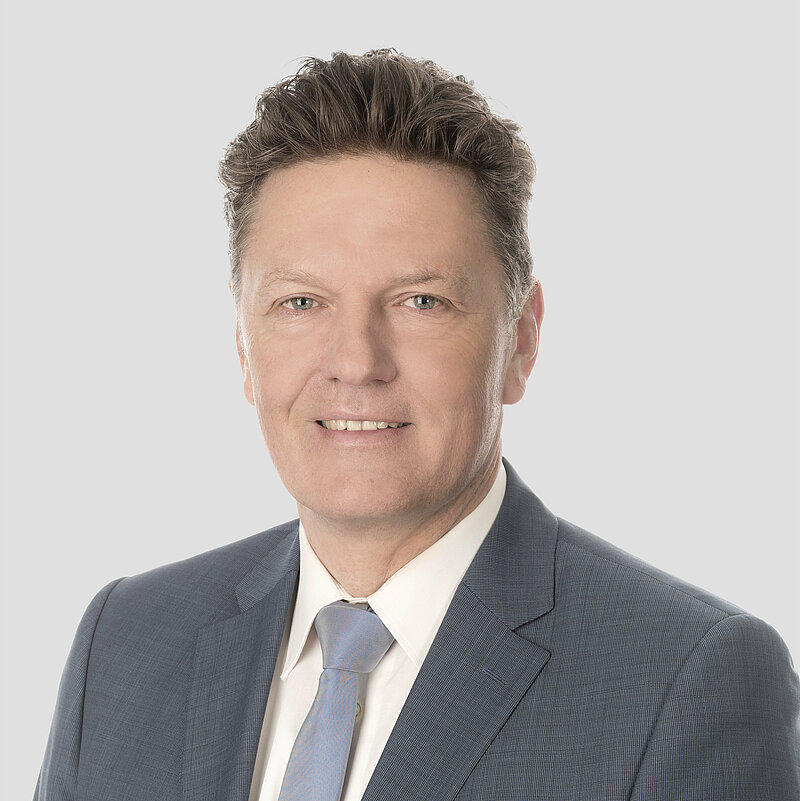
“With investments in new techniques, we’re improving the energy efficiency of Aurubis Bulgaria’s production and reducing the plant’s CO2 emissions by another 2,100 t per year at the same time.”
— Tim Kurth, Managing Director of Aurubis Bulgaria
An emphasis on sustainability: maintenance shutdown in Pirdop
During the more than 40-day routine maintenance shutdown in early summer 2023, about € 60 million was invested in more than 130 maintenance and repair jobs conducted in all of the key production areas of the plant. One clear focus was sustainability and the Group’s target of reducing CO2 emissions from production by 50 % by 2030, such as by optimizing energy efficiency in production. To continue increasing plant availability, a second anode casting wheel was installed to accompany the existing anode furnaces. In addition to Aurubis employees, at times there were more than 900 employees of contractors on-site during this large-scale logistical and technical project, which had been planned since 2021. The project concluded successfully within the timeframe and budget, and in compliance with the highest occupational safety and health standards.
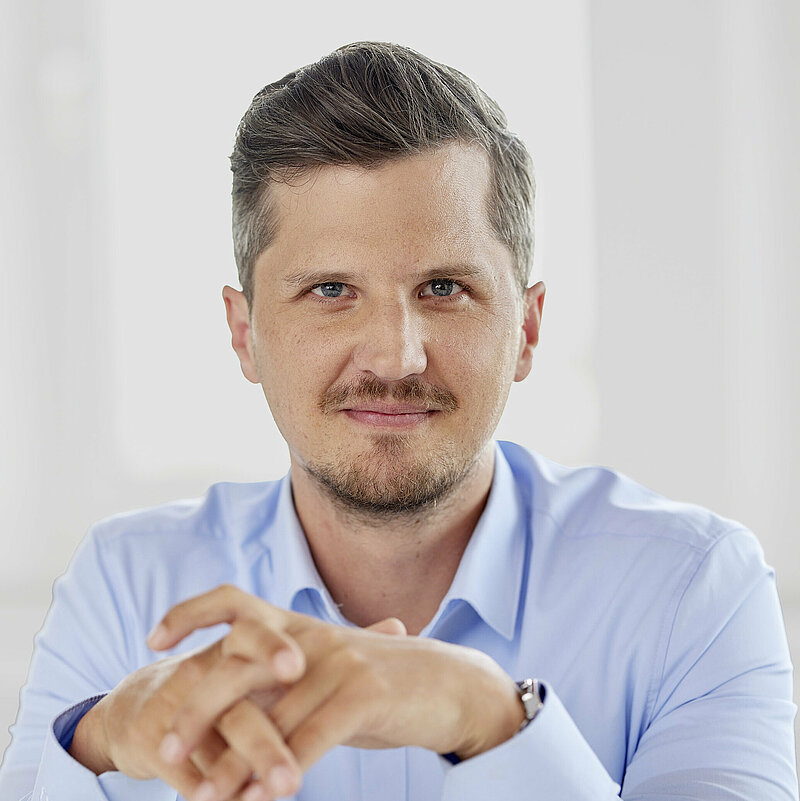
“With the new hydrogen-ready anode furnaces, we’re taking a step into the future and demonstrating: We’re ready!”
— Thies Fingerhut, Project Manager for Anode Furnace 2.0, Aurubis Hamburg
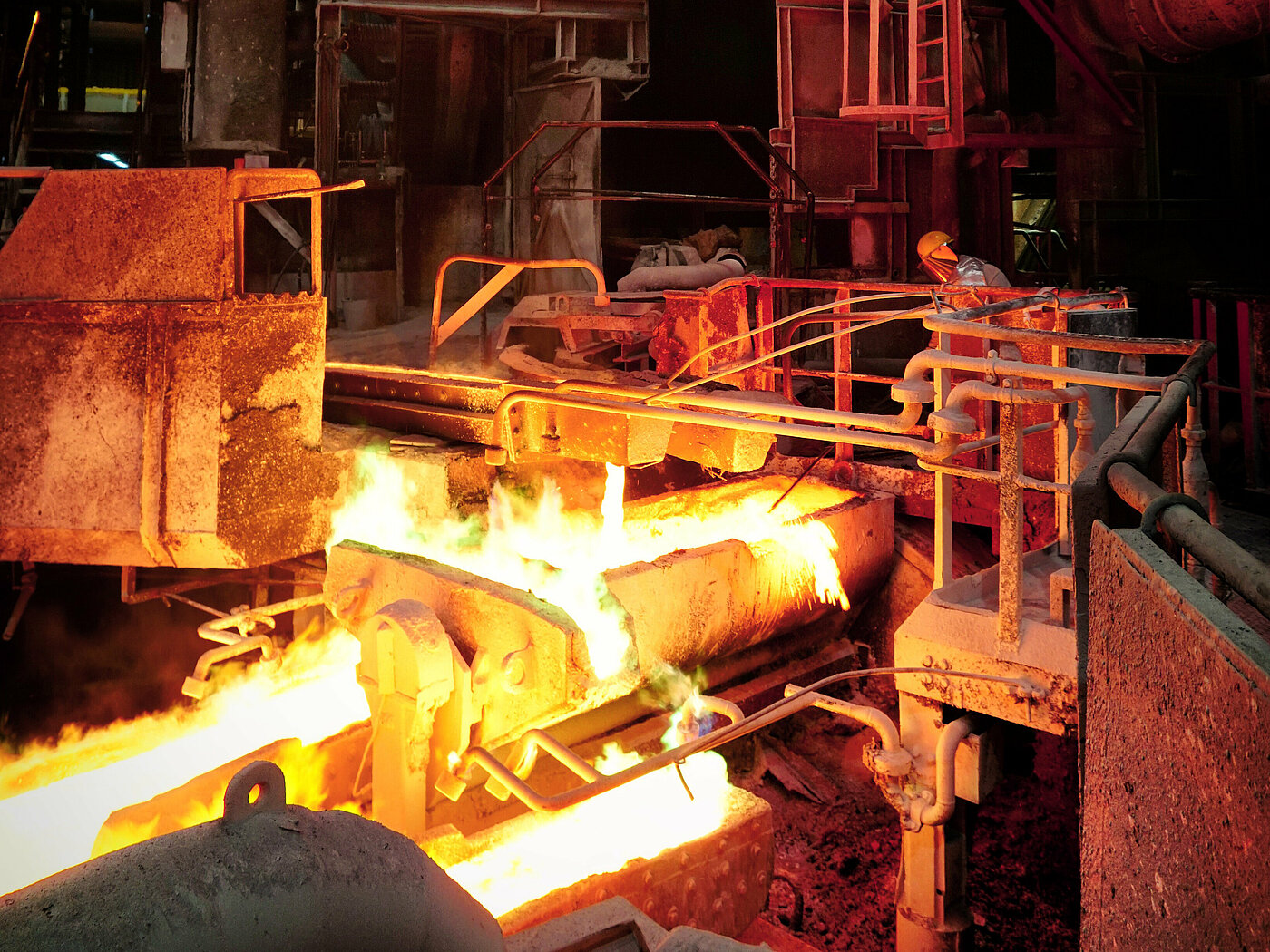
H2-ready as of 2024: anode furnaces capable of using hydrogen in Hamburg
As a company with a nearly 160-year of history, we are always facing new challenges and investing in carbon-neutral copper production. In the coming year, the Aurubis plant in Hamburg will be one of the first copper smelters in the world to use hydrogen instead of natural gas in its anode furnaces, which could lead to an annual savings of 5,000 t of CO2. While the available quantity of green hydrogen at competitive prices can’t yet cover industry’s huge demand, this step marks another milestone in our decarbonization strategy. The facility will already reduce natural gas consumption by 15 %, thanks to the integration of new, more efficient components, which will lead to an additional savings of 1,200 t of CO2 annually.
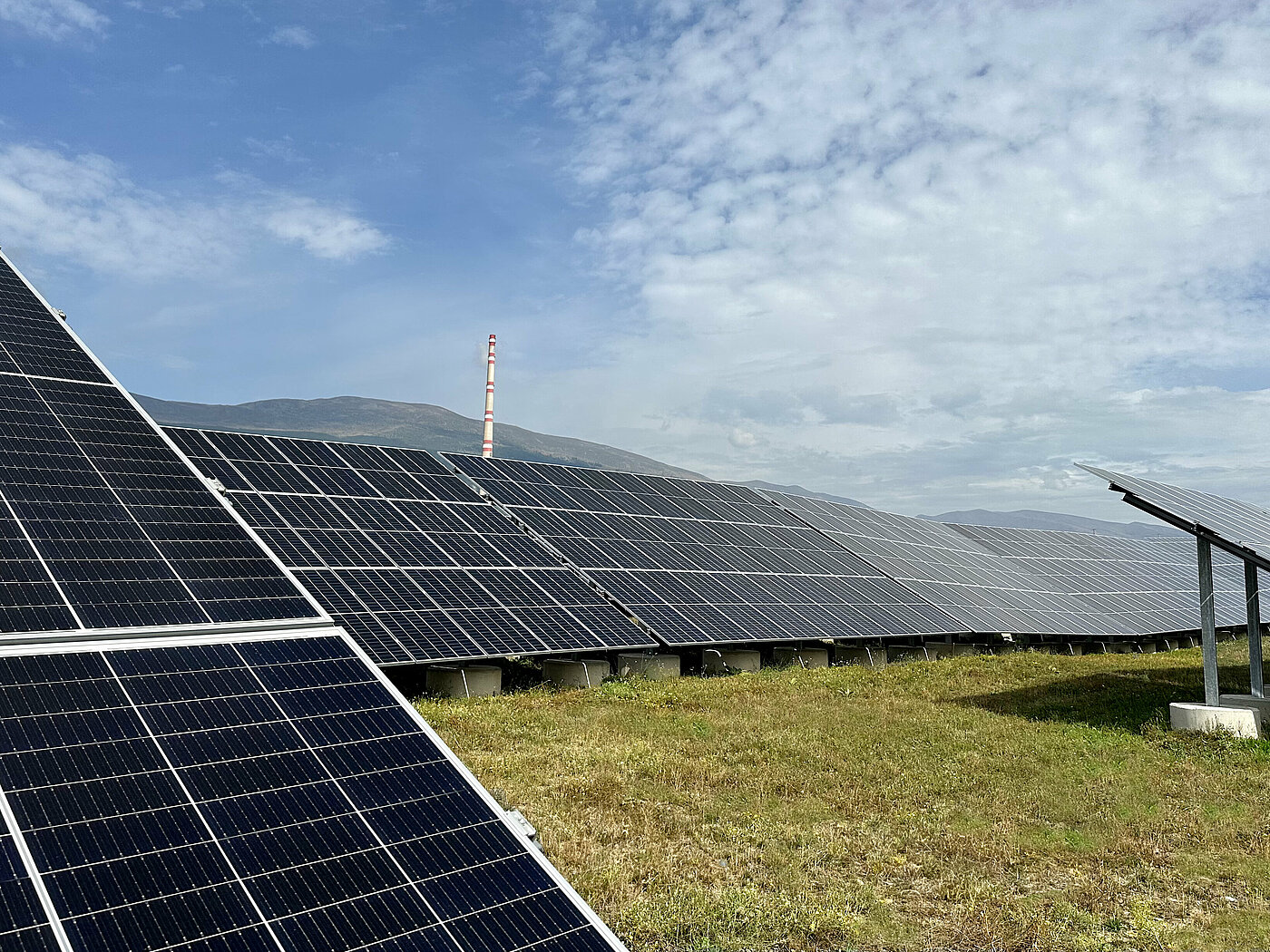
Solar energy: additional facilities in Pirdop
Aurubis Bulgaria’s solar park is an important factor in decarbonizing production in Pirdop, and is already the largest in-house solar park in Bulgaria. We’re now increasing the output of the current facility and the 3rd stage already under construction by an additional 18 MWp (megawatt peak) for a total of around 42 MWp. Once all expansion stages are complete in roughly mid-2025, the total electricity generated will be equavalent to the annual needs of a small town of 15,000 households. Aurubis will thus be avoiding around 28,000 t of CO2 emissions a year.
Industrial Heat 2.0: waste heat from Hamburg
Since 2018, we’ve been supplying Hamburg households with CO2-free waste heat that we extract from a chemical sub-process of copper production and deliver to the neighboring HafenCity East and Rothenburgsort quarters via a roughly 3.7 km long pipeline. In addition to this heat supply, we will be providing up to an additional 20,000 households with heating energy starting in the 2024/25 heating period, saving another 100,000 t of CO2 per year for the city of Hamburg. The Industrial Heat flagship project at the Aurubis Hamburg site drew strong national and international attention. The second stage of this highly complex project will be executed in spring 2024 during the routine scheduled maintenance shutdown in the Hamburg plant, and is the biggest project of its kind in Germany.
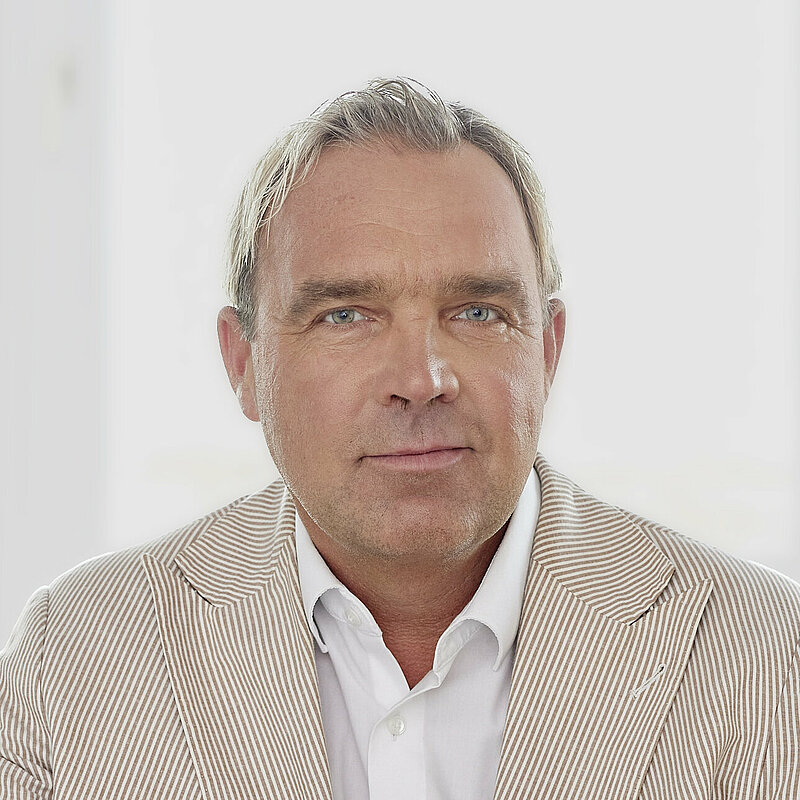
“Aurubis is a forerunner in decarbonization. Our Industrial Heat flagship project is the biggest undertaking of its kind in Germany.”
— Michael Jordan, Aurubis Hamburg Plant Manager

Flagship project: Industrial Heat at the Aurubis Hamburg site.
1. Aurubis
Modification of a copper production sub-process for the use of carbon-free industrial heat (enough to heat 20,000 households)
2. Thermal energy storage
Innovative short-term storage to homogenize industrial heat for use in the district heating network
3. Spaldingstrasse
Feed-in of the industrial heat to Wärme Hamburg’s city-wide district heating network
4. Customers
Delivery of carbon-free industrial heat, with a CO2 reduction of up to 100,000 t per year
Sustainable processes: additional Copper Mark certifications
Following the plants in Pirdop, Hamburg and Lünen, this year Aurubis Olen became the fourth site in the smelter network to be awarded the internationally recognized Copper Mark quality seal. In addition, our site in Stolberg received the Copper Mark in the “Fabricator” category in June 2023, the first processor of rolled copper products to do so, and Aurubis Beerse also started the extensive process this year. We actively pursue the development of sustainable and responsible supply and value chains in the raw materials industry. We revised our Business Partner Screening process for this purpose as well. It now also fulfills the requirements of the Copper Mark regarding responsible sourcing as a criterion for responsible mineral supply chains. In February 2023, we were also one of the first companies in the world to commit to the new Copper Mark Chain of Custody Standard, the first standard that will cover the entire copper supply chain.
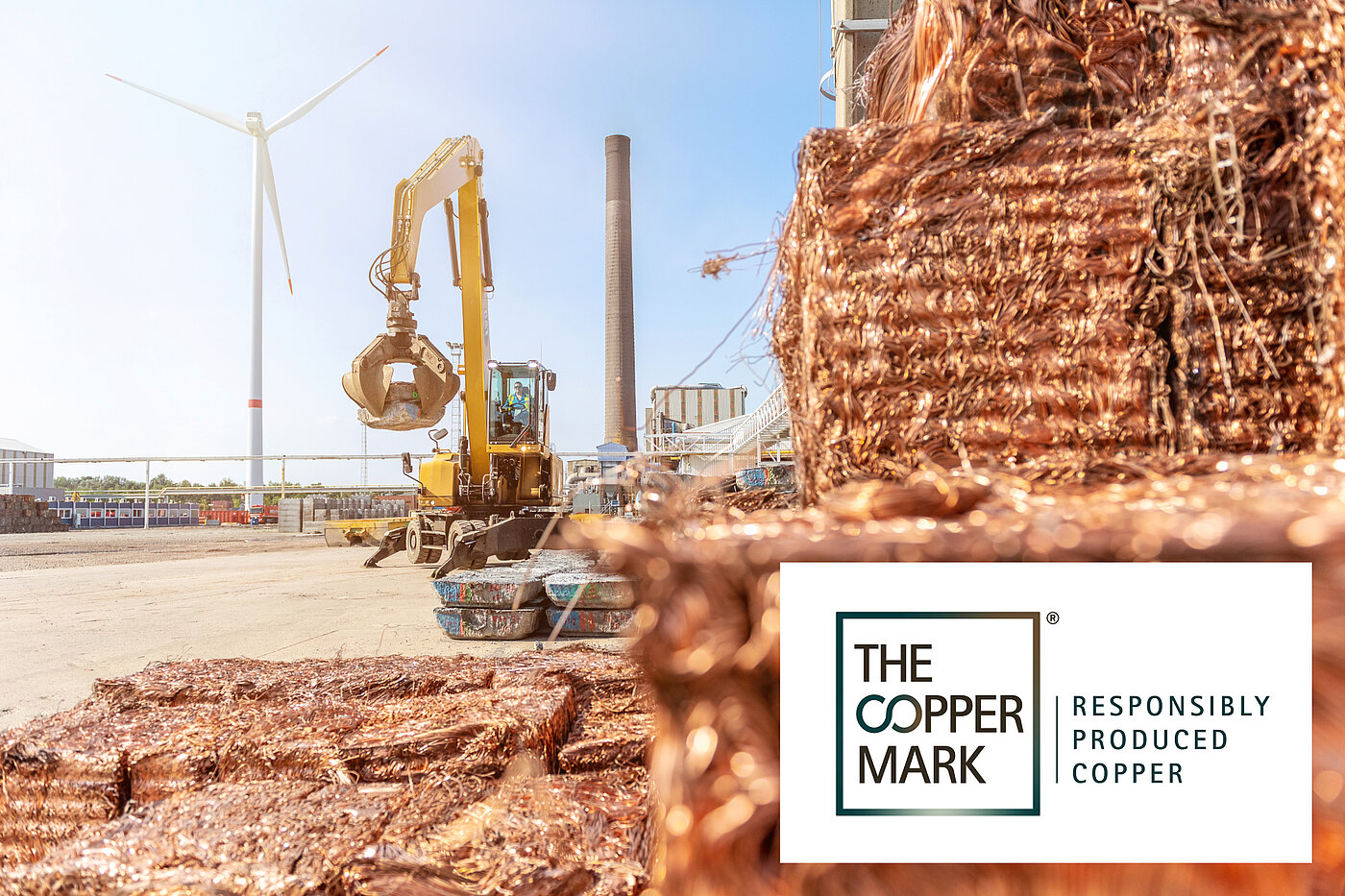
Responsible: partnerships for sustainable copper sourcing
To develop sustainable copper production from primary materials, the actors across the entire value chain have to work together and adhere to shared standards. In early 2023, as part of the German-Chilean Raw Materials Partnership, we signed a memorandum of understanding with the Chilean company Codelco, the largest copper producer in the world. The shared target: promoting collaboration and communication to develop a responsible copper value chain. In November 2022, a similar memorandum of understanding was signed with the multinational mining company Anglo American based in London (UK). There, too, we’re pursuing the goals of fulfilling the growing demand for metals of the future through sustainable copper mining and sourcing, utilizing shared expertise for new technological solutions, and making the entire copper production process more transparent.
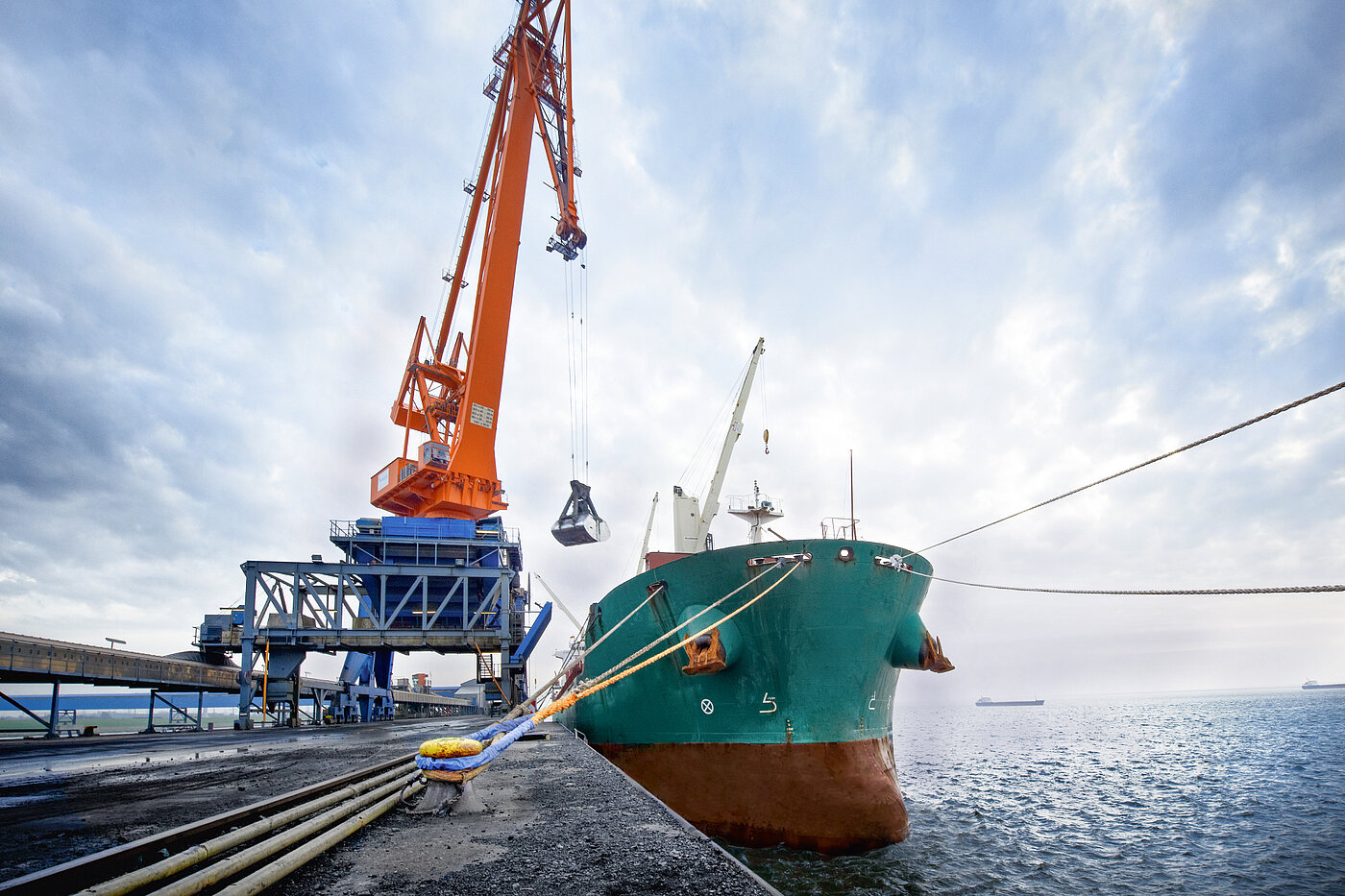
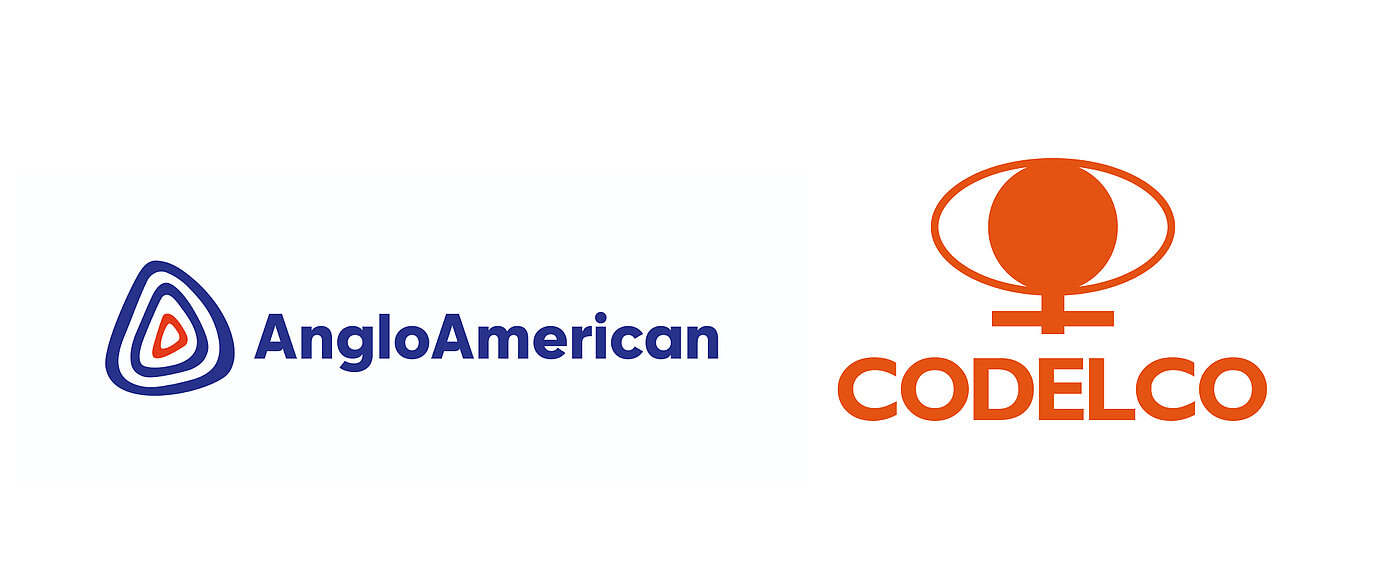
Security: innovative precious metals processing in Hamburg
A new facility for processing precious metals, the Precious Metals Refinery (PMR), will be constructed by the end of 2026. With this investment, we are raising the bar with innovative process technology and systems engineering and the highest standards for plant and precious metals security and occupational safety. Precious Metals Hamburg comprises the entire precious metals processing chain in one closed security area. Newly developed metallurgical processes will boost efficiency, reduce throughput times, and lower operating costs by around 15 %. The expanded production capacity in precious metals will enable us to lay the groundwork for implementing additional projects from our growth strategy.
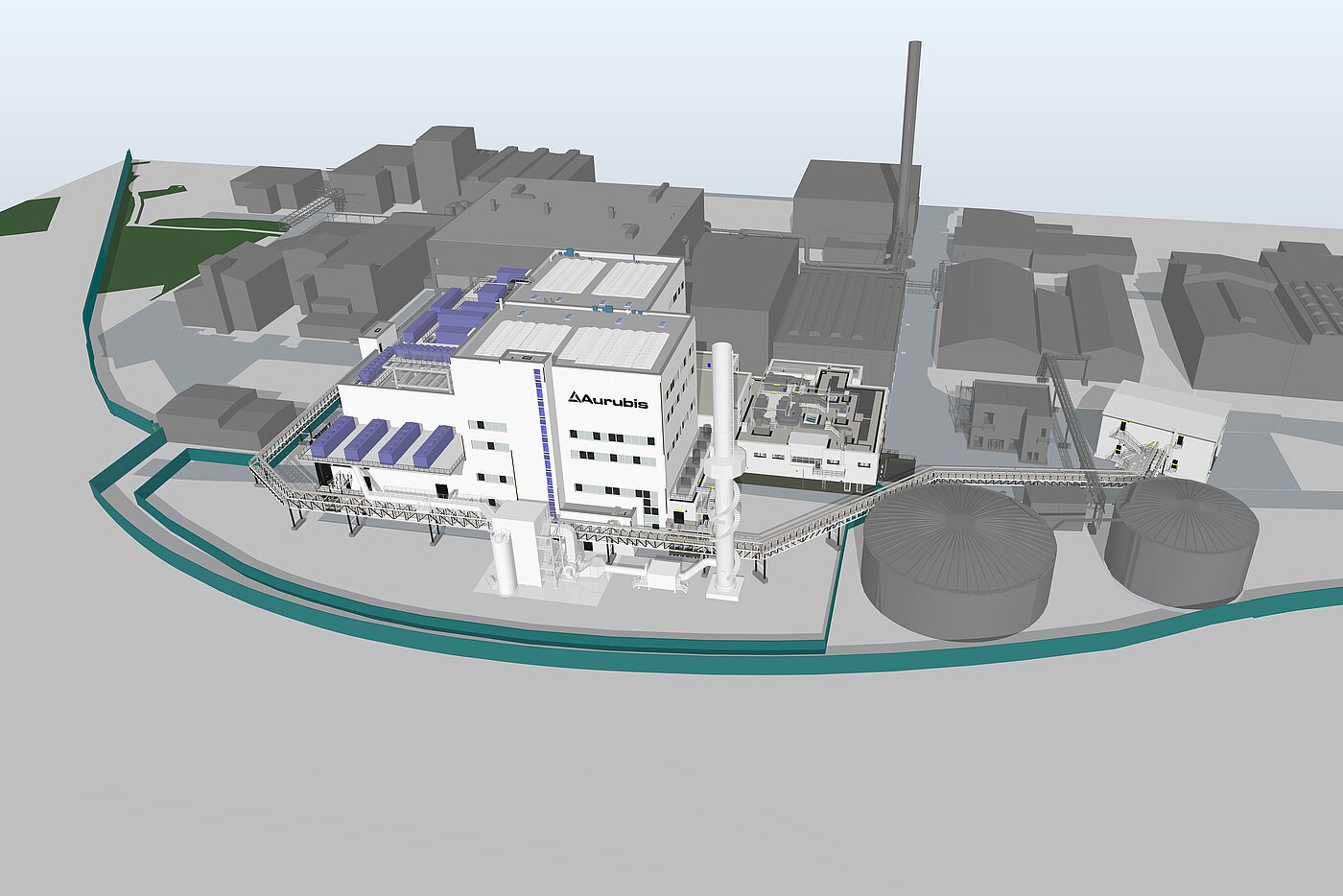
Environmental protection: improved slag processing in Pirdop
At its site in Bulgaria, Aurubis is investing in the improved treatment of slag from copper refining. The new process involves cooling the slag in pots, as opposed to pits as it is now. As of commissioning in 2026, Aurubis will significantly exceed the industry standard in environmental protection and will have achieved dual goals: a considerable reduction in diffuse emissions and increased work safety for this process. Metal recovery will also increase by about 500 t of copper each year. Overall, it’s a project that once again demonstrates how responsibly and efficiently we transform raw materials into value while conserving resources.
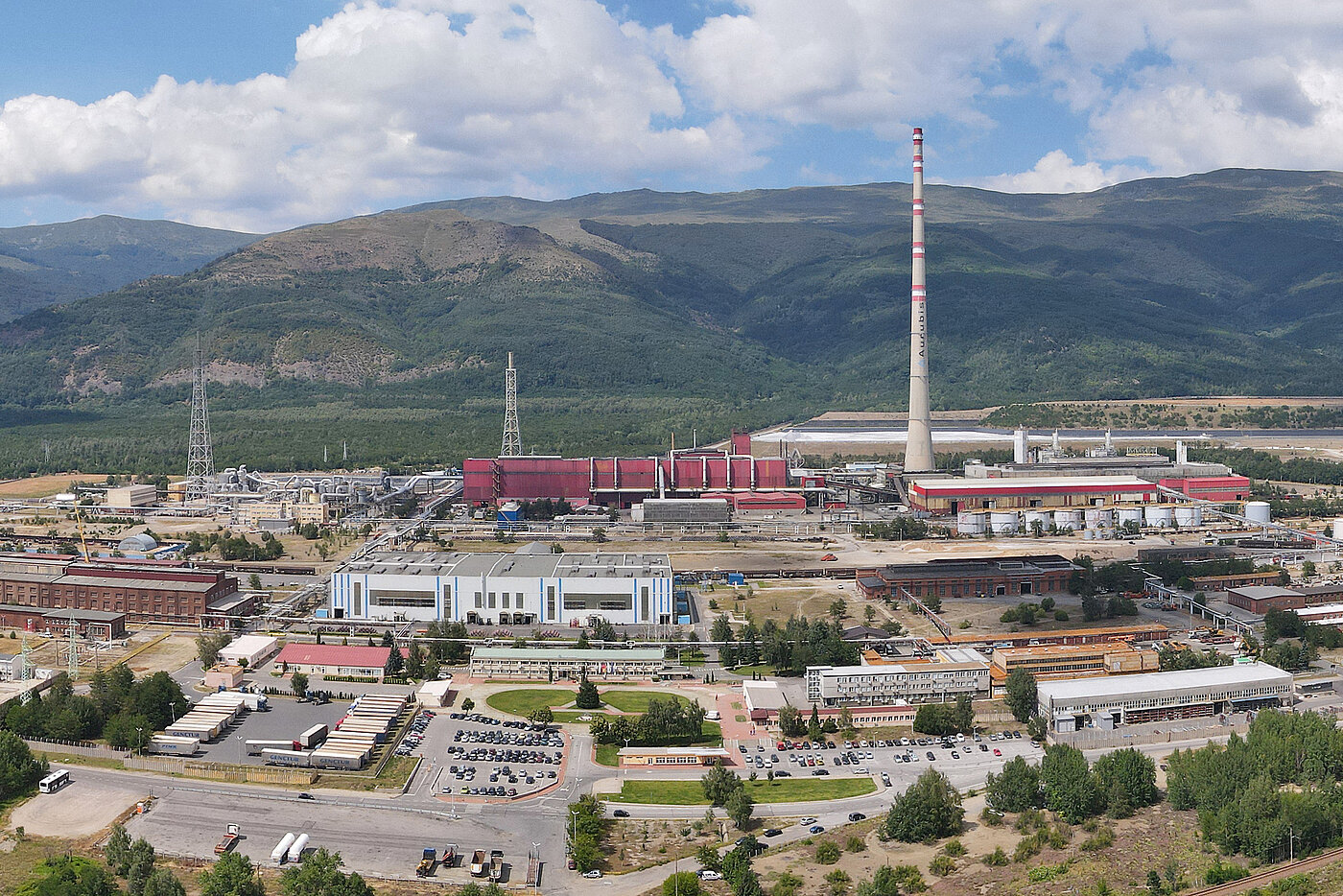