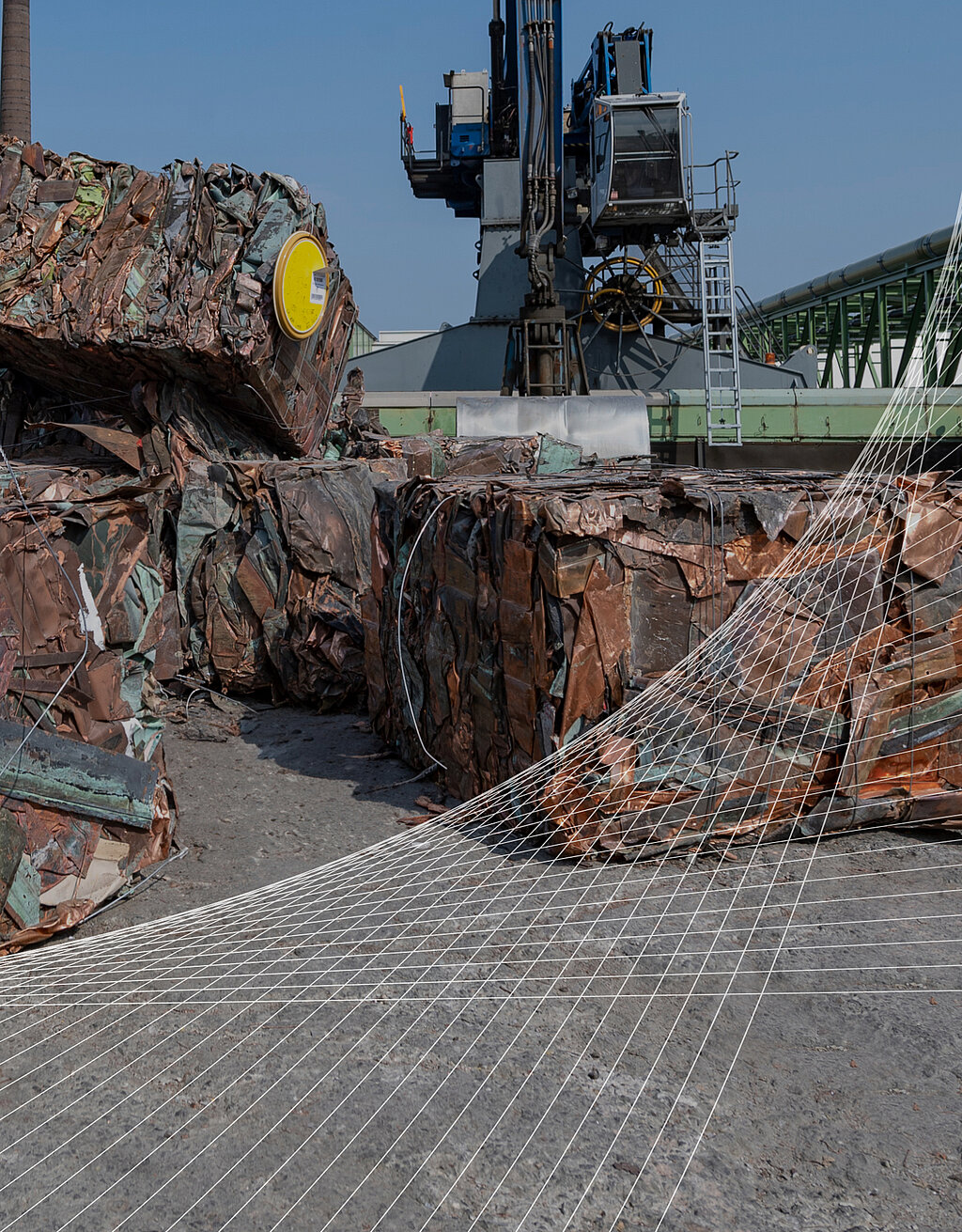
More metals
More metals for a sustainable world
With large-scale investments in the US and Europe, we’re promoting the development of the circular economy.
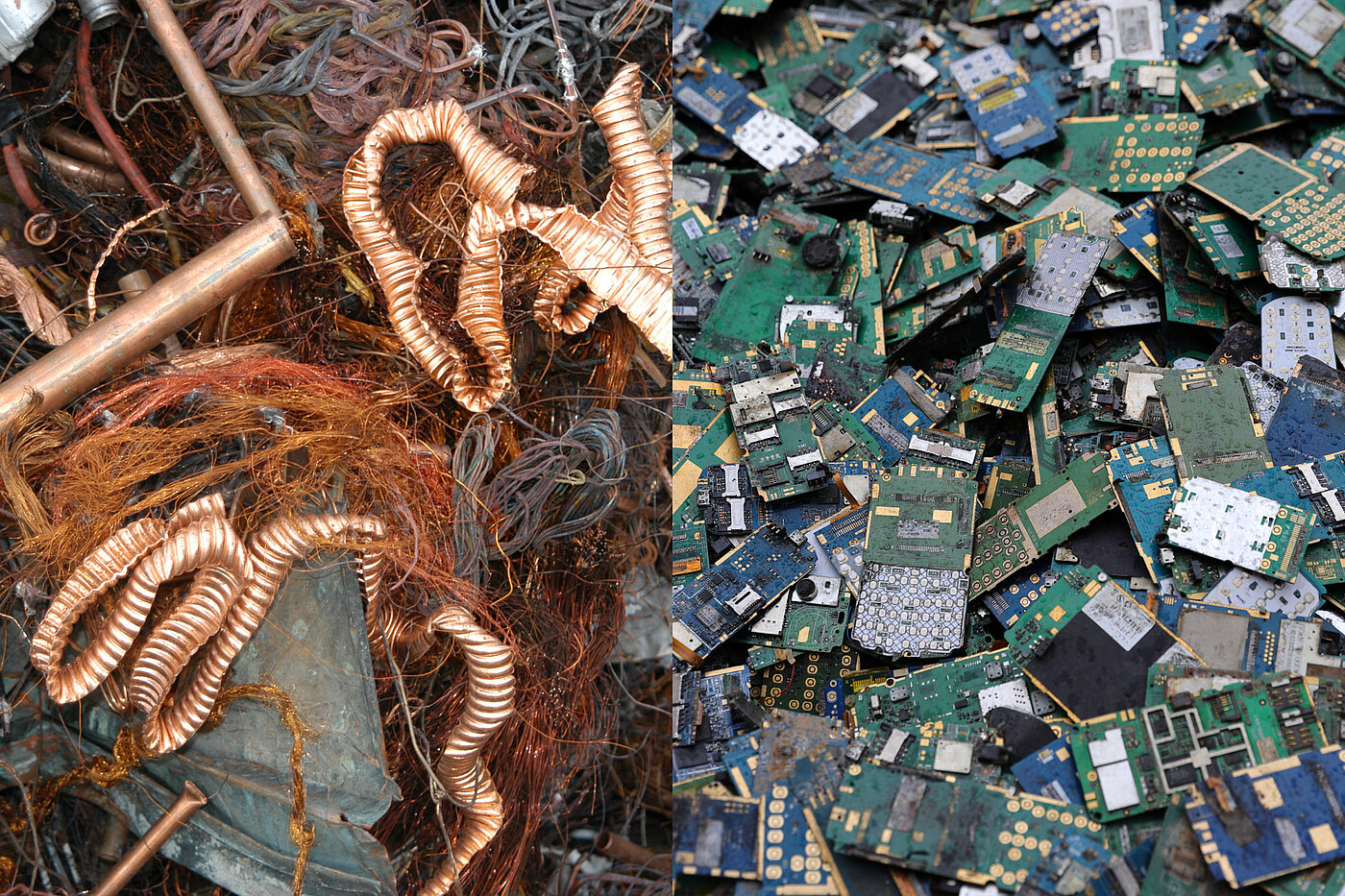
Annual volume of recycling material to be processed at Aurubis Richmond as of 2026
180,000 t
Circular economy
For Aurubis, growth primarily means producing more metals. More metals for a green and digital future. More metals for a sustainable world. Recycling and the circular economy play a central role here — as a response to rising future demand for raw materials. After all, metals are at the core of the circular economy. Our main product, copper, can be processed over and over without a loss of quality, for example. Using existing resources on-site also saves huge quantities of energy and greenhouse gas emissions.
We already process more than a million tons of complex recycling materials, and we want to continue growing in the area of recycling. As one of the world’s biggest copper recyclers, we are using our extensive expertise to develop our capacities and our efficiency in metal recycling even further. The objective of our strategy is for Aurubis to offer the entire value chain real solutions for the circular economy.
Valuable raw materials
One of the central projects: Aurubis Richmond. With the construction of the first US recycling smelter specialized in multimetal recycling, we are opening up a highly attractive new market with an annual recycling material volume of more than 6 million t. Until now, most US electrical and electronic scrap has been exported, landfilled or remained uncollected, and local industry has lost valuable critical and strategic raw materials. The supply of complex recycling materials has gotten a boost due to a growing awareness for sustainability in the US, and declining export rates. In our new facility in the state of Georgia, we can annually process 180,000 t of recycling materials, like e-scrap, into new raw materials. The heart of the process is a state-of-the-art procedure for processing complex recycling materials in order to recover copper, nickel, tin, zinc, precious metals, and platinum group metals in additional stages.
Aurubis Richmond is breaking new ground — and making a significant contribution to more sustainability and supply chain security in the US economy. “Our ambition is to make additional investments in the value chain in the US in the future,” David Schultheis, Managing Director of Aurubis Richmond, says. “Our sites in Europe will also benefit from the new plant’s output: There will be even more co-products and intermediates from copper production that have to be specially processed and refined. To sum it up, the plant in Georgia will complement and broaden our integrated international smelter network with an attractive new site — and diversify our business and project portfolio beyond Europe.”
Our objective for the US: Aurubis plans to become the largest fully integrated producer of copper from recycling materials in North America. In doing so, we will gradually expand our capacities along the entire value chain. Aurubis Richmond is the foundation for this, and not only from a timing perspective. The uniqueness of the project lies in its construction concept: Aurubis Richmond is the first plant that we’re realizing using a modular principle. The modular recycling system we’ve developed allows us to add further facilities and components tailored to the future demands of the new market. An innovative concept that provides a high degree of plannability and maximum flexibility in a booming segment. Nevertheless, in the future we want to use the modular system in established markets, too: as a model for additional growth projects at other Aurubis sites.
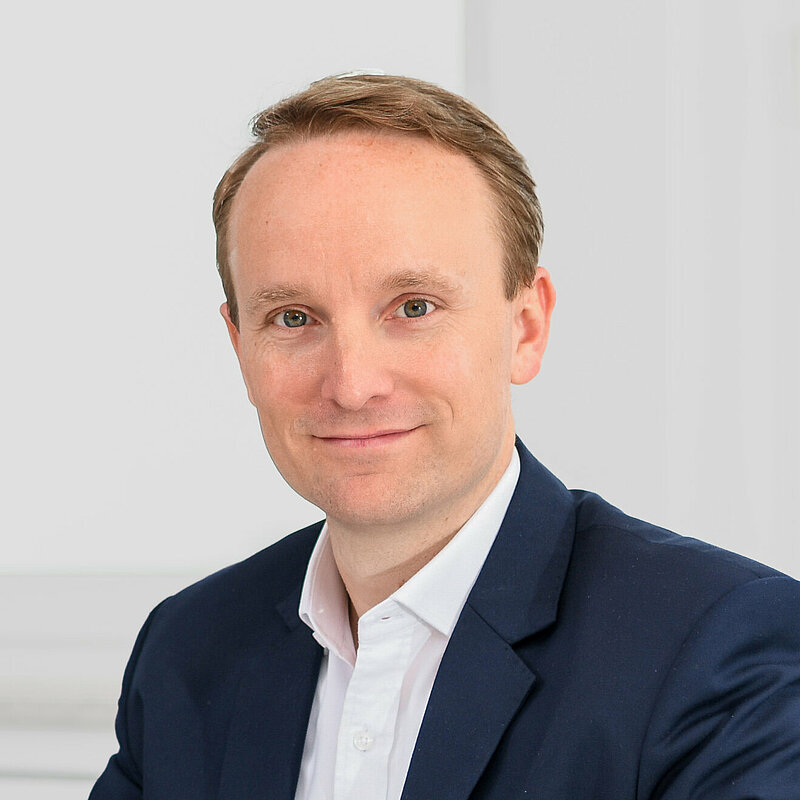
“To sum it up, the plant in Georgia will complement and broaden our integrated international smelter network with an attractive new site — and diversify our business and project portfolio beyond Europe.”
— David Schultheis, Managing Director Aurubis of Richmond
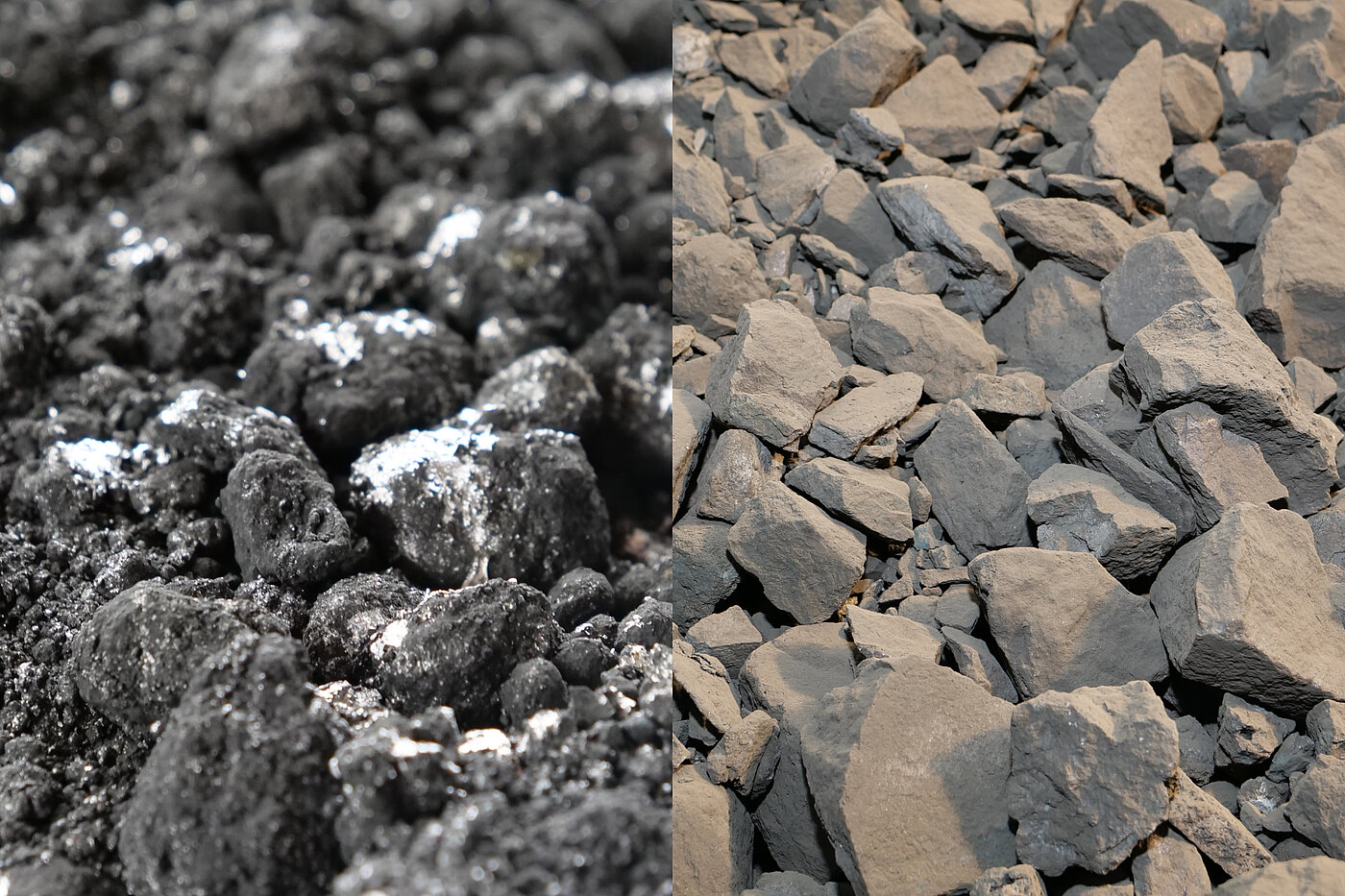
Putting all materials to use
First and foremost, more metals means making our material flows and processing methods even better. With our metallurgical expertise, we keep pushing forward to use resources fully, and in a way that creates value. We believe sustainability and economic efficiency go hand in hand. We want to generate marketable products from all input materials, profitably leverage intermediates and co-products, and avoid residues and waste.
Complex Recycling Hamburg (CRH) at the Aurubis headquarters will set an example starting in 2025. The project centers around an exceptional facility that will allow us to considerably strengthen our capacities for recovering metals from intermediates from copper production. One of these intermediates is copper-lead matte consisting of copper, lead, sulfur and precious metals. Until now, this complex material has been sold to other companies because it can’t be fully processed using conventional metal industry facilites.
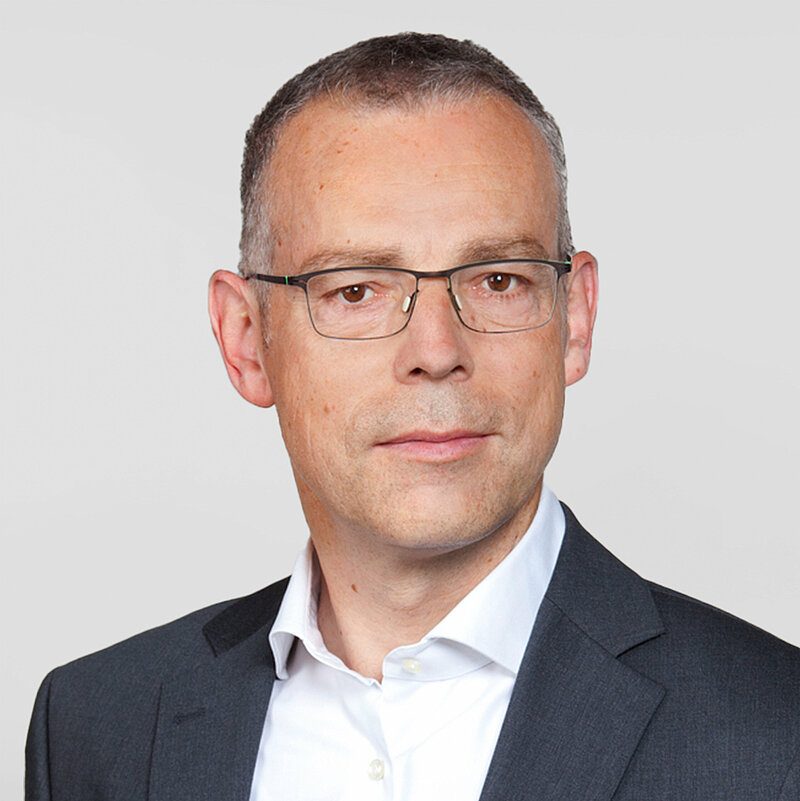
“No other growth project optimizes as many valuable material streams and is as strongly integrated into our smelter network as CRH.”
— Jürgen Jestrabek, Project Manager of Complex Recycling Hamburg
External input materials for CRH
~32,000 t p.a.
Production start
2nd half of 2025
With CRH, however, we’ll be able to process copper-lead matte ourselves in the future, and recover valuable new raw materials from it: blister copper, sulfur dioxide, and lead oxide. We can then feed the blister copper into our copper cathode production, process the sulfur dioxide into saleable sulfuric acid in our sulfuric acid facility, and use the lead oxide in our production processes, as lead is a carrier material for many precious metals and a key factor in recovering and recycling valuable raw materials.
Using everything, and turning it into the best — Aurubis’ metallurgical expertise makes this sustainable approach possible. “The extraordinary thing about Complex Recycling Hamburg is that the technology unites the separation and processing of valuable raw materials in one facility,” Project Manager Jürgen Jestrabek explains. “CRH takes the circular economy to a new level: We’re creating an ecosystem that employs the zero-waste approach, even within the company’s own processes. In the future, we’ll be able to process all intermediates ourselves, leaving nothing behind. With CRH, we’re strengthening our core business with particular intensity. No other growth project optimizes as many valuable material streams and is as strongly integrated into our smelter network as CRH.”
The processes get an efficiency boost at the same time: The new technology makes intermediate steps between separation and processing unnecessary, as everything goes directly into one facility. This means shorter processing times — together with higher capacities. By expanding the portfolio, Aurubis can continue profiting from its own intermediates, and even process material from other companies with CRH in the future. CRH has good competitive prospects. And not just because Aurubis is one of the few metal producers worldwide with this type of technology, but also because the enormous growth in demand for industrial metals guarantees the project a solid foundation for growth.
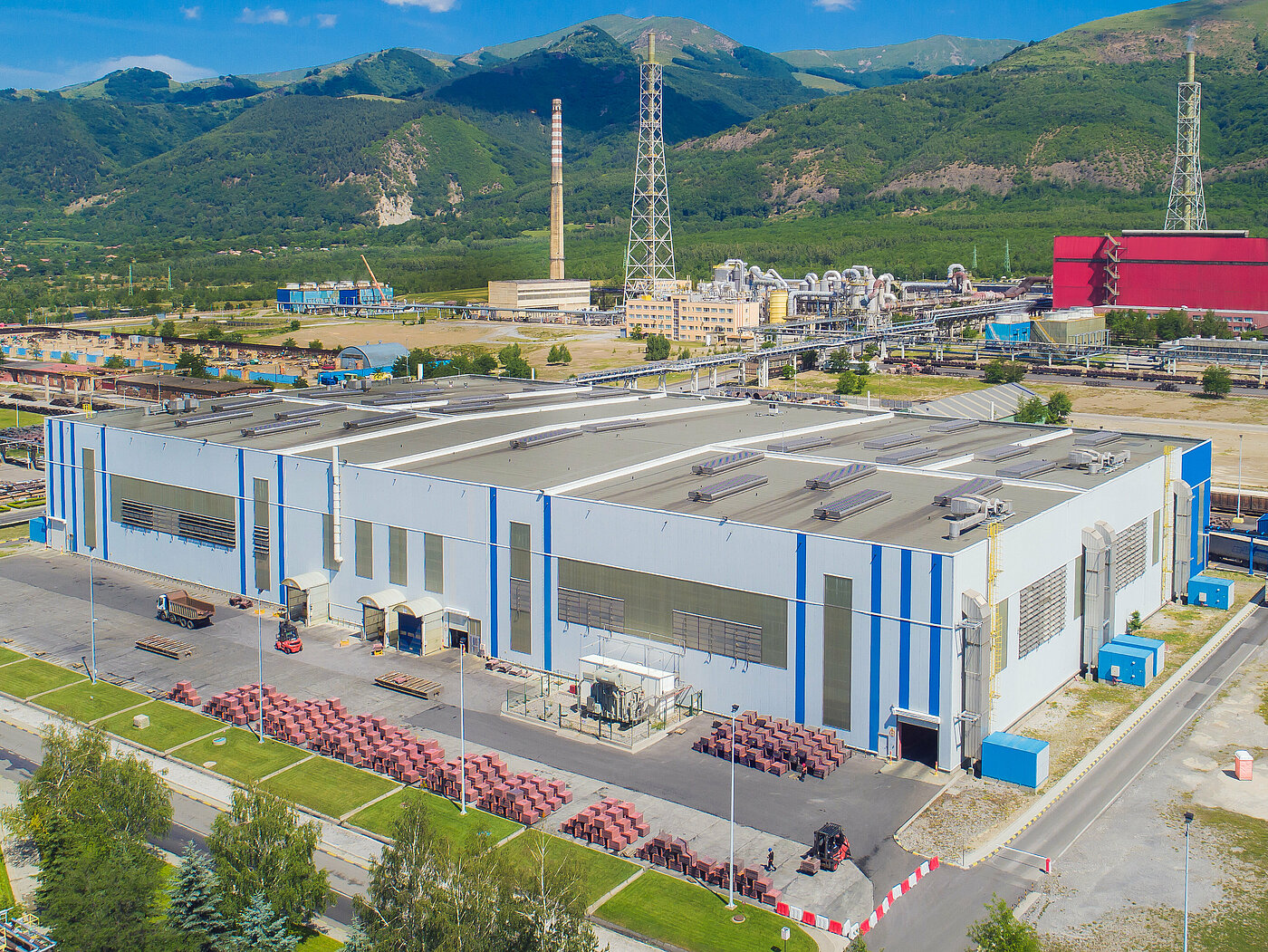
Three advantages at once: tankhouse expansion in Pirdop
A bigger supply for a booming market, leaner processes within the Group, a better environmental footprint — our Pirdop tankhouse investment project checks three important boxes at once. The tankhouse is the final refining stage in copper production. By expanding the facility at the Bulgarian site, we’re strengthening our core business first and foremost: Copper cathode output in Pirdop will increase to 340,000 t per year.
More refined copper from European production helps cover burgeoning demand in the region’s industry. Furthermore, regional production contributes to the European Union’s goal of reducing its dependence when it comes to crucial raw materials. And not least, metals “made in Europe” are produced in accordance with the highest environmental standards. Our own environmental footprint is also shrinking: In the future, we will be able to process all locally produced copper anodes directly in Pirdop instead of transporting some of them to other Aurubis sites as we currently do. This optimizes material flows in the Group, reduces logistics costs — and lowers our CO2-footprint.
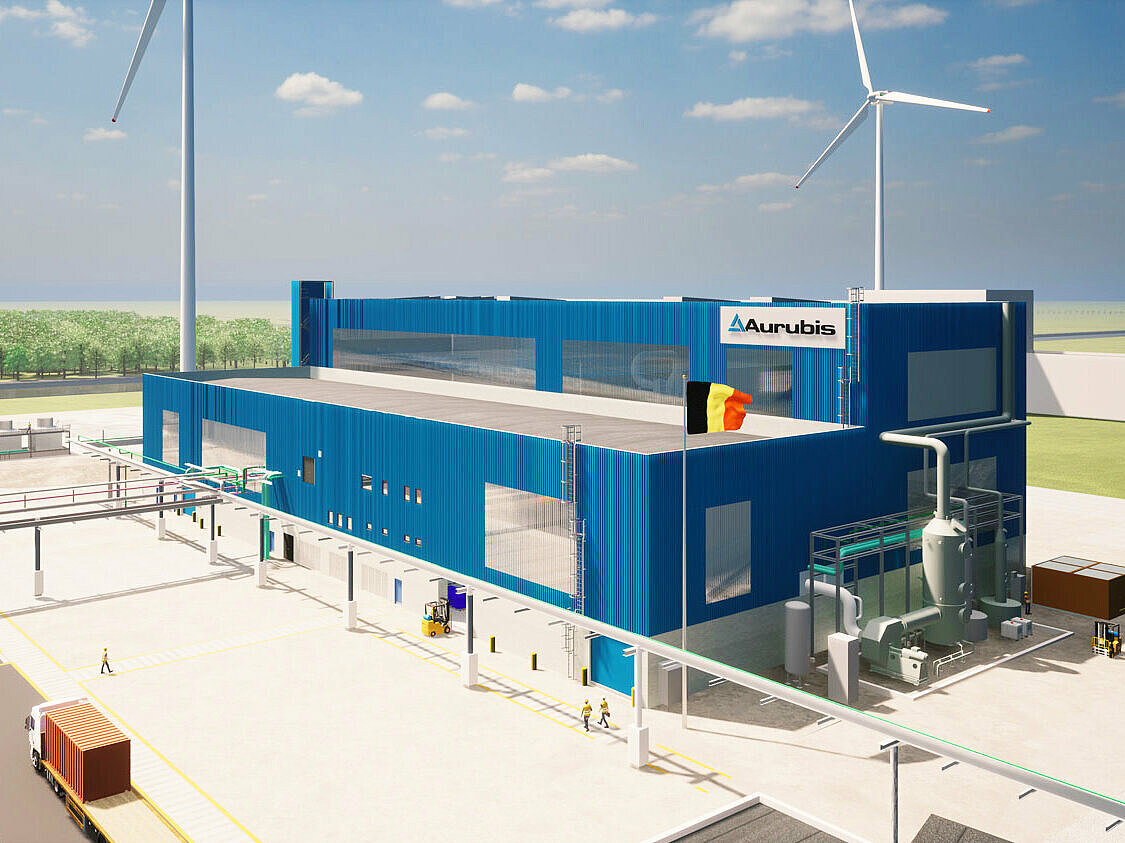
Using all our potential: BOB and ASPA in Belgium
Potential for new raw materials is everywhere. In the future, our plant in Olen, Belgium, will be recovering important new resources from the electrolyte used in metal production. BOB makes it possible: Bleed Treatment Olen Beerse, a new, state-of-the-art facility that draws out valuable raw materials such as nickel and copper from the electrolyte that accumulates in metal production in Olen and Beerse (both in Belgium). With BOB, Aurubis is taking on another part of the multimetal value chain and optimizing the Group-wide material flow. Another benefit: The new facility makes production faster and more efficient. But BOB contributes to our sustainability targets first and foremost: We will recover valuable metals and reinforce our responsible approach to resources.
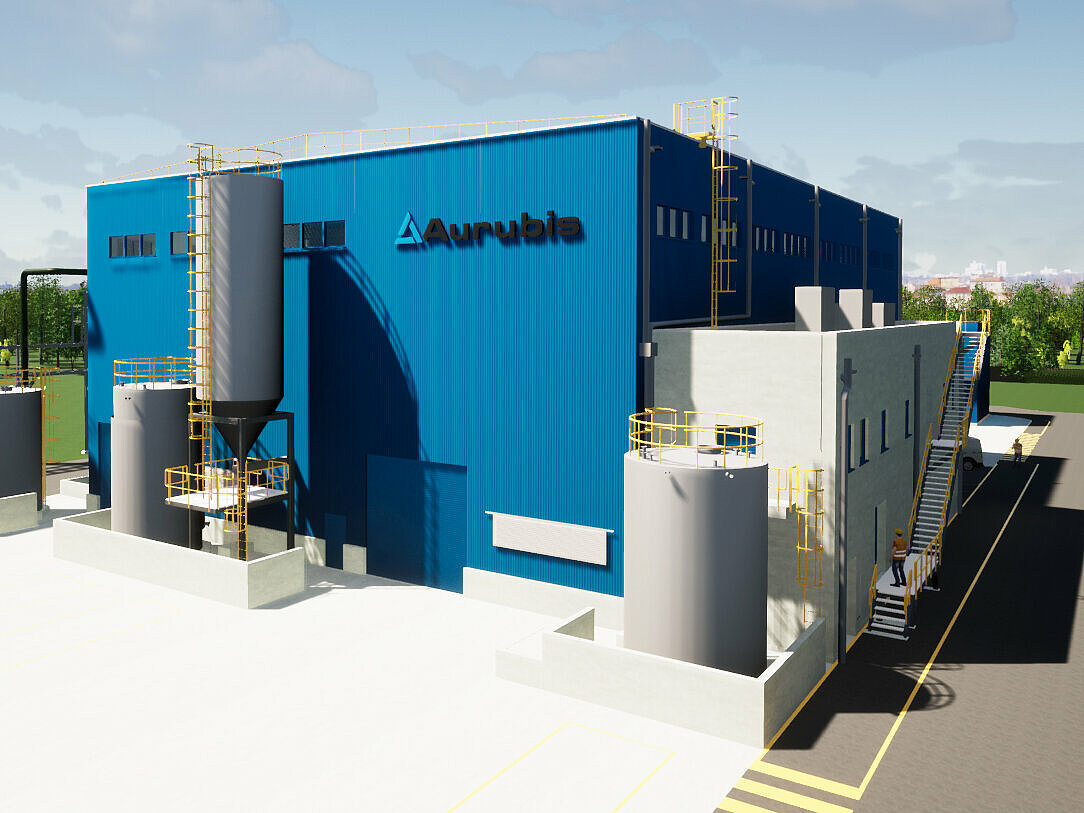
At the Beerse site, too, we’ll soon be utilizing raw material potential even more intensively: With a process developed in-house, we’re improving anode slime processing with a few key steps. This intermediate from copper production contains precious metals, such as gold and silver, as well as tin. With our new Advanced Sludge Processing by Aurubis (ASPA) hydrometallurgical procedure, raw materials can be recovered from anode slime in an even shorter time. The new facility takes metal recycling to the next level: It draws out as many components as possible, as quickly and efficiently as possible — directly on site in the plant. Another important contribution to closing waste cycles and avoiding transports — key elements for us in developing a sustainable circular economy.